Authored by Eluozo SN
Abstract
This paper monitor the rate at which marshal stability experienced improvement through modifiers with shell ash, these are filler that play a tremendous role in engineering properties of bituminous paving mixes. The study tries to improve the asphaltic materials applying these modifiers, the application of conventional, cement, lime and stone done are used as fillers. But for this study, an attempt has been made to access the effect of non-conventional filler (snail shell ash) the study applied modeling and simulation, this concept try to predict the variation of marshal stability at different percentage of shell ash, the predictive values generated parameters that are validated with experimental data, the values of both parameters observed to be stability and OK and it implies that it meant the criteria for asphalt institute for Mix design. The study from the predictive developed parameters between predictive and experimental values are 6.14 and 6.95 7.3 and 7.1 and 6.1 and 6.25, The results of asphaltic concrete showed that at 6.5% of filler content, the generated simulation validated with experimental parameters satisfied the standard of Marshal Properties. Thus, snail shell at 6.5% snail shell content of asphaltic concrete.Keywords: Mathematical model; Marshal stability; Modified asphalt
Introduction
Bitumen is byproducts of the distillation process of crude oils. They are black, oily, viscous, flammable materials. Bitumen was used throughout prehistory as a sealant, an adhesive, building mortar, and waterproofing. Ancient Egyptians utilized bitumen in the embalmment of their mummies, after 1100 BC. The word from which mummy is derived “mum” means bitumen in Arabic and Persian [1]. Being an organic material, bitumen can be affected by temperature, oxygen, and ultraviolet radiation. These external factors cause it to aged and consequential stiffening of the asphalt mix. Ageing of binder within an asphalt mix can have positive action by increasing both cohesion and stiffness, which improves the resistance to permanent deformation and the load-bearing capacity. At the same time, it has a negative effect by reducing the flexibility of the pavement that leads to more possibility for cracks especially by fatigue [2,3]. Ageing of bitumen in asphalt mixes could be divided into short and long term ageing. Shortterm ageing occurs during the mixing and construction process as a result of loss of volatile components and oxidation of bitumen. The long-term ageing takes place through the whole service life of the road via further oxidation of the in-place material (Airey, 2003). The molecules in bitumen can be divided according to their sizes into large molecular size, LMS, (asphaltenes), medium molecular size, MMS, (resins) and small molecular size, SMS, (oil). Noureldin (1995) studied the changes in molecular size distribution caused by oxidation via thin film oven test (TFOT). It was revealed that the changes in molecular size distribution can be described as increases in LMS percentage and viscosity and decreases in MMS, SMS, and penetration. Also, ageing by oxidation makes the resins and oily components transform into asphaltenes (Noureldin, 1995). The increasing proportion of asphaltenes, plus the fact that the maltenes phase is not sufficient to disperse asphaltenes, elevates viscosity of bitumen.Fillers are fine material and are usually considered as modifiers and are not considered in the gradation of aggregates [4]. Fillers in HMA have a lot of advantages. In addition to filling the voids, they reduce moisture susceptibility (hydrated lime filler), increase bond between aggregate and asphalt and increase the stiffness by adding of rigid materials in less rigid matrix Buttlar et al. (1999). Fillers play an important role in reducing the optimum asphalt content [1]. However, having too much filler in hot mix asphalt can reduce the interaction between aggregates and binder as coating of the aggregates by fillers will increase the amount of binders hence weakening the [1,3]. These fillers differ in surface texture, shape, surface area, void content, mineral composition and other petrochemical properties [5]. Rigden voids’ content describes the volume percentage of voids in a dry compacted filler sample. Higher Rigden voids leads to higher stiffening of binder. Fillers tend to increase the resilient modulus of asphalt mixes [6] .However, most of the strength of HMA is attributed to the surface contact between the aggregate particles. Excessive amount of fillers will result in an increase in the bitumen content and can result in a weak asphalt mix [1].
Theoretical Background
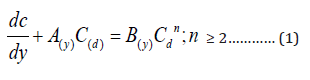
Where A(y) and B(y) are function of y

Divided by (1) through by Cd-n we have obtain
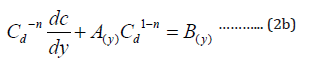
Let β = Cd-n

Multiplying Equation (2a) through by (1- n)
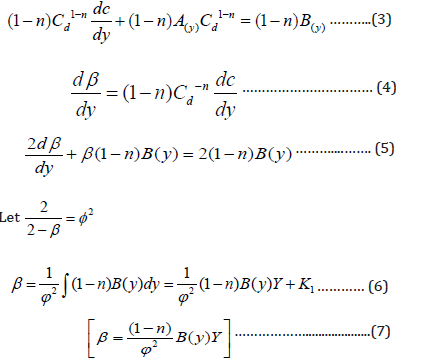
Materials and Method
The materials which were used in this study were all locally available. Snail Shell Ash was sourced from Mile One Market in Port Harcourt, Rivers State [7-10]. The samples were burnt in an open air and milled using an edge milling machine to obtain the required ashes used as filler.Material used
The materials used in this study are1. Aggregates (Fine and Coarse Aggregate)
2. Bitumen (Asphalt Cement)
3. Filler (Snail Shell Ash)
4. Cement
Details of materials
Aggregate: Aggregate is a collective term for same, gravel and crushed stone mineral material in their natural processed state. Fine aggregate defined by (AASNTO M-147) as natural or crushed sand passing the number 10 sieve sand mineral particle passing number 200 sieve. Coarse aggregate defined by (AASNTO M-147) as hard, durable particles or fragments of stone, gravel or slag retained on the number 10 sieve [8-12].Usually coarse aggregate has a toughness and abrasion resistance requirement. The coarse and fine aggregate were separated to various sizes. Coarse and fine aggregate used in this research was brought from material shop at Mill 3, Diobu Port Harcourt, Rivers State. The coarse and fine aggregates were sieve and recombined in laboratory in order to produce identical controlled gradation.
Bitumen (Asphalt cement): Bitumen is an oil based substance. It is a semisolid hydrocarbon product produced by removing the lighter fractions (such as liquid petroleum gas, petrol and diesel) from has crude oil during the refining process. It is black or brown in color possess water proofing and adhesive properties. It is collectively known as refined bitumen. The asphalt mixture contains approximately 5% bitumen at ambient temperatures bitumen is a stable semi solid substance. The bitumen used for this research project was collected from Setraco Nigeria ‘Limited Site, Enugu-Port Harcourt expressway, Okiegwe Imo State. It was graded bitumen with a checked confirmed penetration of 60/70 and specific gravity of 1.06 (3.1).
Filler (Snail shell ash): Asphalt institute defined filler as a finely divided mineral product at least 65% of which will pass through a number 200 sieve.
Filler play a dual role in asphalt mixtures, firstly the act as a part of the mineral aggregate by filling the voids between the coarse particles in the mixture and thereby strengthen the asphalt mixture. Secondly when mixed with asphalt, fillers form mastic a high consistency binder [13-15]. The type and amount of filler used in hot asphalt mixture would be affecting the properties of the mixed.
The filler used in this experiment is Snail Shell Ash. (SSA), the physical properties of this mineral filler were shown in 3.2.
Laboratory test carried out on the aggregate
The aggregates (which includes sand and crushed rock) used in this research were subjected to various laboratory tests in other to assess their physical characteristics and suitability in the road construction. The tests carried out are Sieve Analysis and specific gravity.Gradation test (Sieve analysis): Sieve analysis for both coarse and fine aggregate was carried out and their corresponding particles size distribution was plotted on a log graph in Appendix D.
a. Apparatus
• Rings-Brass, square shouldered rings
• Ball steel balls
• Ball centering guides
• Bath- A squat, heat resistant glass vessel
• Ring holder
• Thermometer
• Reagent
b. Test procedure: The softening point test is essentially a ball and ring test which involves placing a steel ball on a mass of bitumen contained in a brass ring and heated in a water bath until the bitumen is soft enough to allow the ball fall through a height of 25mm. the temperature of the water at which this occurs is known as the softening point of the bitumen.
Penetration test
a. Apparatus
• Penetrometer
• Needle for bitumen test
• Additional weight (50gm)
• Two sample ready for use with steel plate
• Hot plate for melting
• Stop watch
b. Test procedure
The penetration test involves the determination of the extent to which a standard needle penetrates a well prepared sample of bitumen under definitely specified conditions of temperature, load and time. A penetrometer was used which allowed a 100g needle to move vertically downward without friction and the distance moved by the needle in units of tenths of millimeters was recorded as the penetration of the bitumen. Hence the procedure was repeated four times and the average value of the penetration obtained and recorded for further analysis. The bitumen used for this experiment was collected from and has confirmed penetration of 60/70. The physical properties of asphalt cement were tested according to the standard specification.
Marshal tests
The marshal test procedure involves the preparation of several samples of the asphalt concrete in form of moulds for the purpose of determining its characteristics such as bulk density, bulk specific gravity, stability, flow and voids in the asphalt concrete mix. Several test samples were first of all prepared in varying percentages of bitumen content and data curves on these samples were plotted to determine the asphalt concrete optimum bitumen content. The marshal procedures are further explained.Sample preparation (Unmodified mix): The asphalt concrete mix samples were first of all prepared to determine the optimum bitumen content. This was done by varying the bitumen content in each mix from 0%, 1.5%, 2.5%, 3.5%, 4.5%, 5.5%, 6.6% increment of asphalt content. In order to provide adequate data, two test samples of the asphalt concrete mix were prepared for each bitumen content percentage used.
Each briquette used as a test specimen to determine the OBC was made of the design mix proportion of the various ingredients such as sand, crushed rock and bitumen to arrive at a total weight of 1200g of the mix. Each briquette was 63mm thick by 100mm diameter size. During the preparation of the asphalt concrete samples, the aggregates were weighed for each batch mix and heated in an oven for 24 hours.
The aggregate batch mixes were placed in a bowl and the bitumen was added to the batch and mixed together on heating with a stove. After heating the mix to 1150C due to the bitumen viscosity, the mix was put in the mould and compacted at 1050C with 50 blows on both sides (specified for medium traffic design) of the mould using a rammer freely falling at 450mm height and having a weight of 6.5kg. The compacted samples were allowed to cool, after which they were removed and kept for 24 hours before other tests were carried on the samples to determine its bulk density, stability, flow and voids.
Optimum bitumen content (OBC) determination: The optimum bitumen content from the control mix (unmodified sample) was obtained by taking the average of the binder contents at maximum stability, maximum unit weight (Density) and median limit of air voids. This is the asphalt content required for optimum performance and suitable for best stability.
Modified sample preparation (Using snail shell ash filler): The preparation of the cement modified asphalt concrete samples followed the same procedure as for the unmodified (0% filler) samples as already described. However, there were slight modifications during its preparation which are as follows:
• The weight of the bitumen was kept constant at its optimum bitumen content of the overall weight of mould.
• The snail shell ash was introduced in varying contents of 1.5%, 2.5%, 3.5%, 4.5%, 5.5%, and 6.5%.
• The snail shell ash was introduced with aggregate and heated in the mixing bowl prior to the addition of the bitumen.
Three samples of the snail shell ash modified asphalt concrete were prepared to ensure a more accurate result.
Bulk density test: The bulk density test was performed as soon as the freshly compacted samples were cooled to room temperature. The procedure for this test is outlined below:
• Weigh the compacted mould in air
• Soak mould in water (completely submerged) for one hour and weigh in air.
• Soak the mould in water for one hour and weigh in water
• Calculate the bulk density of the mould using the equation below:
e = Wao/(Wa1-Ww)
Eq.3.1
Where e = Bulk density
WWao = Weight of sample in air
Wa1 = Weight of sample in air water after one hour soaking
Ww = Weight of sample in water after one hour soaking
Stability and flow test: The stability and flow tests were carried out simultaneously to obtain stability values in Newton (N) and flow values in millimeters (mm) of the asphalt concrete mix. The marshal testing machine and a water bath are the equipment used for this test. The procedure for the stability and flow tests is as follows:
• Heat the asphalt concrete mould in the water bath for 30 to 40 minutes at 600C constant temperature
• Cleanse the testing head and lightly oil the guiding rods
• Remove the sample from the bath and dry it carefully
• Position the sample in the lower testing head and fit it with upper testing head
• Position the head assembly in the marshal testing machine with the flow meter in position
• Apply the testing load on the sample at a constant rate of deformation of 50mm/minute until failure occurs. The point of failure is the point where the maximum load is obtained
• The load dial reading and the flow meter reading at the point of failure are recorded.
To read more about this article....Global Journal of Engineering Sciences
Please follow the URL to access more information about this article
https://irispublishers.com/gjes/fulltext/development-of-mathematical-model-to-predict-marshal-stability-on-modified-asphalt.ID.000524.php
To know more about our Journals....Iris Publishers
To know about Open Access Publishers
No comments:
Post a Comment