Authored by Dhrubo Jyoti Sen*,
Abstract
A pharmaceutical uncoated tablet must satisfy certain standards to claim it to be a quality drug. The quality of any drug in dosage form is its safety, potency, stability, patient acceptability and compliance. The quality of tablet needs to be designed from the product development stage. Quality control test for uncoated tablet is strongly related to final product quality because checks performed during production in order to monitor and if necessary, to adjust the process to ensure that the product conform to its specification are the key for the good or excellence quality of a tablet. The main purpose of quality control test for uncoated tablet is to produce a perfect finished product quality control (FPQC) test for tablet are performed with specific quality control test or parameters within acceptance limit or not. The aim of this to study in process quality control test carried for uncoated Paracetamol & Nimesulide.
Keywords: Quality control; quality control test or parameters for uncoated tablets (Paracetamol & Nimesulide); batch details; Analytical data for compressed tablet; Analytical data for finished stage; specification
Introduction
Quality Control (QC): It is a small part of QA and it is concerned with Sampling, testing and Documentation during manufacturing and also after completion of manufacturing. It is the monitoring process through which manufacturer measures actual quality performance compare it with standards and find out the causes of deviation from standard to ensure quality product not once but every time [1].
• Quality control involves testing of units and determining if they are within the specifications for the final product. The pur/ pose of the testing is to determine any needs for corrective actions in the manufacturing process. Good quality control helps companies meet consumer demands for better products [2].
• Why there is a need to perform Quality Control test for tablets?
• To ensure safety, potency, efficacy, stability, patient acceptability and patient compliance of tablet.
• To check whether pharmaceutical tablets satisfy certain standards to claim it to be a quality drug or not.
• To check that the quality parameters are within the acceptance limits or not [3] (Figure 1).
Quality Control test for tablets
1) Official test
• Weight variation test
• Dissolution test
• Disintegration time test
2) Unofficial test
• Thickness
• Hardness
• Friability
Official test


Weight Variation Test: According to the USP weight variation test is run by weighting 20 tablets individually calculating the average weights and comparing the individual tablet weights to the average. The value of weight variation test is expressed in percentage. The following formula is used: Weight Variation=(Iw–Aw)/ Aw×100%. Where, IW=Individual weight of tablet; Aw=Average weight of tablet. As per USP the tablet complies with the test if not more than 2 of the individual masses deviate from the average mass by more than the percentage deviation [4] (Figure 3).
Disintegration Test: The USP disintegration apparatus consist of 6 glass tubes that are 3 inches long, open at the top, and held against a 10-mesh screen at the bottom end of the basket rack assembly. To test for disintegration time, one tablet is placed in each tube and the basket rack is positioned in specified medium at 37 ± 2 °C such that tablet remains 2.5 cm below the surface of the liquid on their upward movement and descend not closer than 2.5 cm from the bottom of the beaker. A standard motor driven device is used to move the basket assembly containing the tablets up and down through distance of 5 to 6 cm at a frequency of 28 to 32 cycles per minute. Perforated plastic discs may also be used in the test. These are placed on the top of tablets and impart an abrasive action to the tablets. The discs may or may not be meaningful or impart more sensitivity to the test, but they are useful for tablets that float. Operate the apparatus for the specified time (15 minutes for uncoated tablet unless otherwise justified and authorized) [5].
Note:
• The disintegration time is not for buccal, sublingual and chewable tablets, because they are directly absorbed.
• No disintegration time for sustained release and controlled release tablets. (Figure 4)
Dissolution Test: The BP or USP dissolution apparatus (Basket apparatus) consist of a cylindrical vessel with a hemispherical bottom, which may be covered, made of glass or other inert, transparent material; a motor; a metallic drive shaft; and a cylindrical basket. The vessel is partially immersed in a suitable water bath of any convenient size or heated by a suitable device such as a heating jacket. The water bath or heating device permits holding the temperature inside the vessel at 37±0.5°C during the test and keeping the bath fluid in constant, smooth motion. For this test according to BP and PhEur place the stated volume of the dissolution medium (± 1 %) in the vessel of the specified apparatus. Assemble the apparatus; equilibrate the dissolution medium to 37±0.5°C. Place 1 tablet in the apparatus, taking care to exclude air bubbles from the surface of the tablet. Operate the apparatus at the specified rate. Within the time interval specified, or at each of the times stated, withdraw a specimen from a zone midway between the surface of the dissolution medium and the top of the rotating basket or blade, not less than 1 cm from the vessel wall. Where multiple sampling times are specified, replace the aliquots withdrawn for analysis with equal volumes of fresh dissolution medium at 37°C or, where it can be shown that replacement of the medium is not necessary, correct for the volume change in the calculation. Keep the vessel covered for the duration of the test and verify the temperature of the medium at suitable times [6].


Unofficial test
Hardness Test: For this test one of the earliest testers was Ketan tablet hardness tester, which is a type of the Monsanto hardness tester to evaluate tablet hardness tester. The tester consists of a barrel containing a compressible spring held between two plungers. The lower plunger is placed in contact with the tablet and zero reading is taken. The upper plunger is then forced against a spring by turning a threaded bolt until the tablet fractures. As the spring is compressed, a pointer rides along a gauge in the barrel to indicate the force. The force of fracture is recorded in kilogram [7] (Figure 5).
Friability test: Friability of a tablet can determine in laboratory by Roche friabilator. For this test twenty (20) tablets are weighed and placed in the friabilator and then operated at 25 rpm for 4 minutes. The tablets are then deducted and weighed. The difference in the two weights. It is determined by the following formula; Friability=( IW–Fw)/IW×100%. Where, IW=Total Initial weight of tablets; Fw=Total final weight of tablets. As stated by USP if conventional compressed tablets that loss less than 0.5 % to 1 % (after 100 revolutions) of their weight are generally considered acceptable [8] (Figure 6).


Discussion
• The quality control testing is assigned to production or quality control depending on the company basis of large scale and small scale.
• The Quality executives evaluate the quality tests of the tablets to pass the products into markets.
• These are regularly checked by the RA and FDA bodies [9].
Aim & Objective
A. Objective:
• To study in process quality control test carried for uncoated paracetamol & nimesulide tablets.
B. Purpose & Scope:
• The purpose is to provide documentary evidence that the manufacturing. Process of uncoated paracetamol tablets is capable to produce the product meeting the predefined Specification and quality attributes.
• The scope of this report is limited to first three commercial batches manufactured of the same batch size and specified equipment’s and control parameters of Uncoated Paracetamol & Nimesulide tablets [10].
Methods
Drug profile
1) Drug profile of paracetamol:
2) Drug profile of nimesulide:
3) Drug profile of paracetamol:
Generic name: Acetaminophen.
Chemical name: N-(4-Hydroxy phenyl)-acetamide, N-(4-hydroxy phenyl)-ethanamide.
Chemical structure: (Diagram 1)
Category: Aniline analgesics
Formula: C8H9NO2.
Molecular weight: 151.163gm/mol.
Melting point: 169°C
Solubility: Soluble in alcohol & water.
Side effects: An allergic reaction, which can cause a rash and swelling. Flushing, low BP and a fast heartbeat-this can sometimes.
Uses: Paracetamol is a common painkiller used to treat aches and pain. It can also be used to reduce a high temperature. It’s available combined with other painkillers and anti-sickness medicines. It’s also an ingredient in a wide range of cold and flu remedies.
Adverse effect of paracetamol: In general, acetaminophen (the active ingredient contained in paracetamol) is well tolerated when administered in therapeutic doses. The most commonly reported adverse reaction have included nausea, vomiting, constipation. Injection site pain and injection site reaction have been reported with the I.V. product [11].
Drug profile of nimesulide:
Generic name: Nimesulide
Chemical name: N-(4-nitro-2-phenoxyphenyl) methane sulfonamide
Chemical structure: (Diagram 2)
Category: NSAID
Formula: C13H12N2O5S
Mol. Weight: 308.31gm/mol
Melting point: 97.5°C
Solubility: Soluble in water at room temperature.
Side effects: Diarrhoea, skin rash, itchiness, dizziness.


Uses: Acute pain, relive pain and swelling of joints and muscle in adults, osteoarthritic pain, symptomatic pain associated with osteoarthritis in adults.
Adverse effect of nimesulide: Avoid consuming alcohol while taking this as it can increase your risk of stomach problems. You may regularly monitor your kidney function, liver function and levels of blood components if you are taking this medication for long time treatment [12] (Table 1-3).
Table 1:Batch details.

Table 2:Product details for uncoated paracetamol & nimesulide tablet in pharmaceutical industry.

Table 3:Equipment details.

Table 4:Assessment of critical process parameters.

Process Flow Diagram: (Figure 7)

Note: This is critical parameters are following in only Welable Healthcare Pharmaceutical company.
Analytical data for compressed tablet:
Compression: During compression, samples from compression machine at optimum speed were collected at the Beginning, middle and end of compression to test Description, Average weight, Weight variation, Disintegration time, Friability, Hardness, Thickness, Diameter and Weight of 20 tablets (Table 5(A), Table-5 (B) & Table-5 (C), Table 6) [13].
Table 5:Batch No: 1710.

Table 6:Batch No: 1717

Table 7:Batch No: 1718
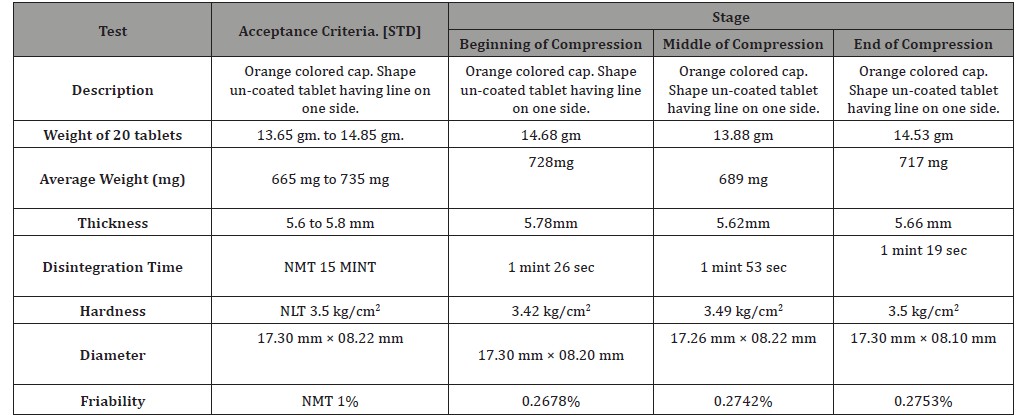
Table 8:Analytical data for finished stage.

Discussion
Weight variation: The variation of weight of individual is a valid indication of the corresponding variation in the drug content. According to the BP the acceptable deviation should not more than 1% for a tablet to be accepted, as shown in the Table-5. All the batches in the study comply with the weight variation test [14].
Friability: The friability test of all the batches ranges from 0.27% to 0.28% and have record of not more than 1% weight loss thus the result is acceptable. As shown in the Table-5. All the batches in the study comply with the friability test [15].
Hardness: The Hardness test is a measure of the compression force required to break a tablet. Hardness of not less than 3.2 kg/cm2 is satisfactory. As shown in the Table-5. All the batches in the study comply with the Hardness test [16-20].
Thickness & DT: The Thickness and DT of the tablets were both in excellent state no significant deviation is observed.
Conclusion
All batches analysed passed the Weight variation, Friability, Hardness, Thickness and DT test. To ensure that established product quality standards are met, these tests must be performed during production (in process control) and verified after the production of each batches batch no: 1710, 1717 and 1718.
To read more about this article....Open access Journal of Chemistry and Biochemistry
Please follow the URL to access more information about this article
To know more about our Journals...Iris Publishers
No comments:
Post a Comment