Authored by Antje Krahmer*,
Abstract
Conductive yarn materials are the basic requirement for the production of heating textiles. In the project, conductive yarn materials with uniform and permanent electrical resistances in the high-ohm range (1-1000 kΩ/m) were developed. The electrical resistances thus achieved in the high-ohm range have a small variation of less than 10 % over 1m and also over 2cm yarn sections, which enables the use of the developed conductive yarns in heating textile surfaces which can be freely cut. The basis is the developed coating technology that involves a polymer coating with conductive additives. Carbon particles and intrinsically conductive polymers were investigated as conductive additives. The conductive polymer coating was applied using coating processes in a laboratory setup and also a pilot plant for up to 4 individual threads with a subsequent thermal activation process.
Keywords:Conductive thread; Heating textiles; Conductive coating; e-textiles; Carbon coating
Introduction
Heating of defined areas in functional clothing and car seats is a popular function of e-textiles. The aim here is to use textilebased heaters to ensure drapability, flexibility and breathability. Heating textiles are among the Smart Textiles for which the global market volume was estimated at around 1.3 billion euros in 2017, according to the short report “FashionTech - Smart Textiles” by the Center for European Economic Research. The global market volume could grow to just under five billion euros by 2022, with the German market likely to account for around 700 million euros of this. A potential market volume of 4.2 billion euros is predicted for Germany alone in 2030, with a global market volume of around 41.4 billion euros [1].
Heating textiles currently available in the market are primarily in the form of flat or roll material. This allows the use in planar surfaces. In the case of non-planar surfaces, available heating textiles reach their limits especially when it comes to equal heat distribution. However, free cutting of heating textile surfaces enables the implementation of customized heating application even for non-planar surfaces, such as shoe insoles, moulded parts or steering wheels. In heating textile surfaces, highly conductive threads as the supply leads (electrode) and high-resistance threads as the heating element are incorporated and interconnected by means of bonding technology. The basic prerequisite for heating textile structures that can be freely cut to size are conductive yarn materials in the high-ohm range with defined and, above all, uniform electrical resistances over a short thread length, e.g. of 2cm. High-ohm conductive yarns currently on the market do not meet electrical uniformity and durability requirements. Moreover, most available conductive filament materials have electrical resistance in the low-ohm range and are a too good conductor for use as heating filaments in freely cut heating surfaces [2-6].
However, the magnitude and the range of variation in the electrical resistance of the high-ohm resistance yarns, as well as their number in the textile structure, have a decisive influence on the achievable heating power and thus on the surface temperature.
By developing a coating technology and applying a thermally activated conductive polymer coating to textile thread materials, disadvantages such as high variations and low reproducibility in the electrical characteristic values are eliminated. The conductive thread developed in the research project “hochohmiger Faden” (INNO-KOM-Ost VF150041) exhibits uniform resistances over the yarn length in the high-ohm range of 1 to 1000 kΩ/ m and an electrical fluctuation range of less than 10 % at 1m or 2cm. Thereby it is predestined for use in heating fabrics that can be freely cut to size. A heating textile based on the developed conductive thread ensures even heat distribution and emission over the entire surface to be heated.
Discussion
Polymer coatings with conductive particles on multifilament yarns
In order to realize electrical resistance in the high-ohm range, various polymer coatings with different conductive additives primarily on polyester-based multifilament yarns were tested. In particular, polyurethane based polymer coatings were used. As conductive additives Carbon particles and intrinsically conductive polymers [7] were added to the polymer coating in various concentrations. Figure 1 shows optical microscopic images of yarn materials coated with various conductive particles and polymers.
The coatings are applied to the yarn using the conventional godet technique for single yarns. In the first step, tests were carried out on a laboratory setup (Figure 2, left). After optimizing the coating formulation and the process parameters, it was possible to scale-up the process to a pilot plant at TITV Greiz (Figure 2, right) in order to implement an economical production method. On the pilot plant, it is possible to coat 4 yarns simultaneously. Hot-air over a yarn length of 30m guarantees the complete drying and fixation of the applied conductive polymer coating.
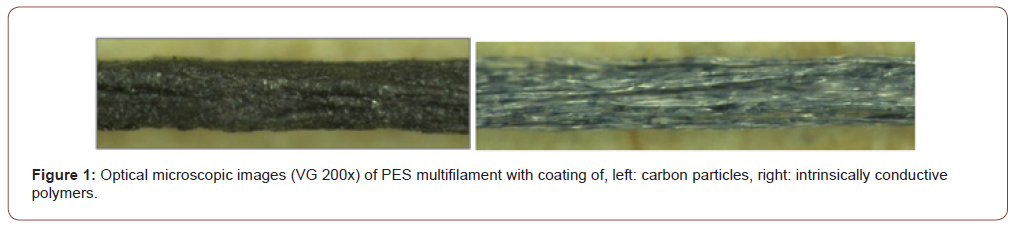
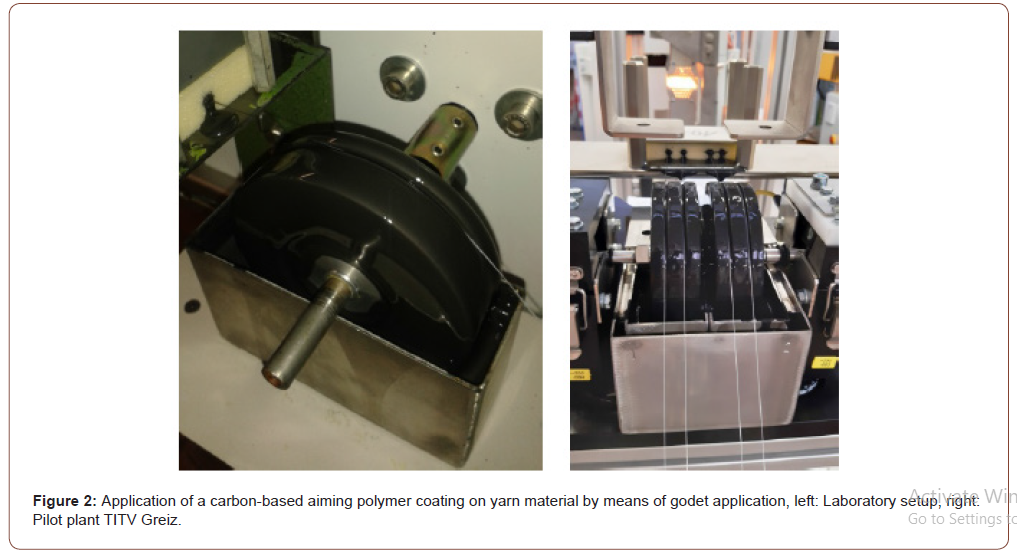
Through carbon-based polymer coating, electrical resistances of 1 -1000 kΩ can be achieved on 1 m filament sections depending on the solids content, the coating layer and the number of coating passes, see Figure 3. For example, after applying the conductive polymer coating (product A) with a solids content of 75 % to a PES multifilament yarn with a fineness of 110dtexf36, an electrical resistance of about 313 kΩ/m and a percentage variation of 4.1 % are achieved after 4 coating passes. With lower solids content of the polymer coating, a higher electrical resistance of about 1160 kΩ/m is realized. The standard deviation here is also about 4 %. Therefore, the developed technology can be adapted to the requirements of the electrical resistance.
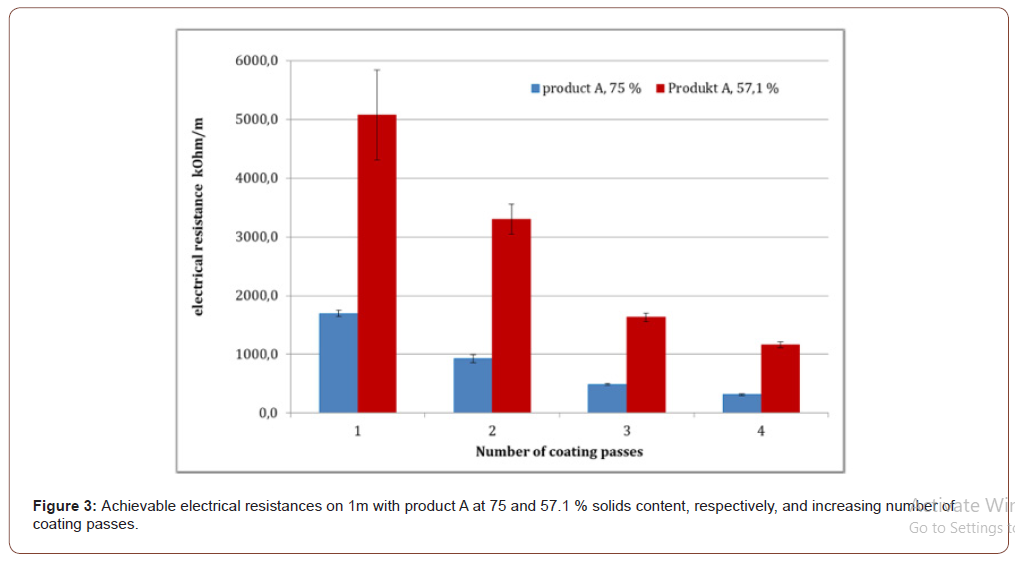
On 2cm sections of filament, the electrical resistance at 75% solids content of the product after 4 passes is 5.6 kΩ and the variation percentage is 9% (Figure 4).
The images in the scanning electron microscope (magnification 200) show an increase in the applied carbonaceous polymer coating, see Figure 5. After the 1st coating pass, a homogeneous conductive layer is not yet visible, which results in the high electrical resistances. With a higher number of coating passes, the conductive layers become more closed and thus the electrical resistance decreases.
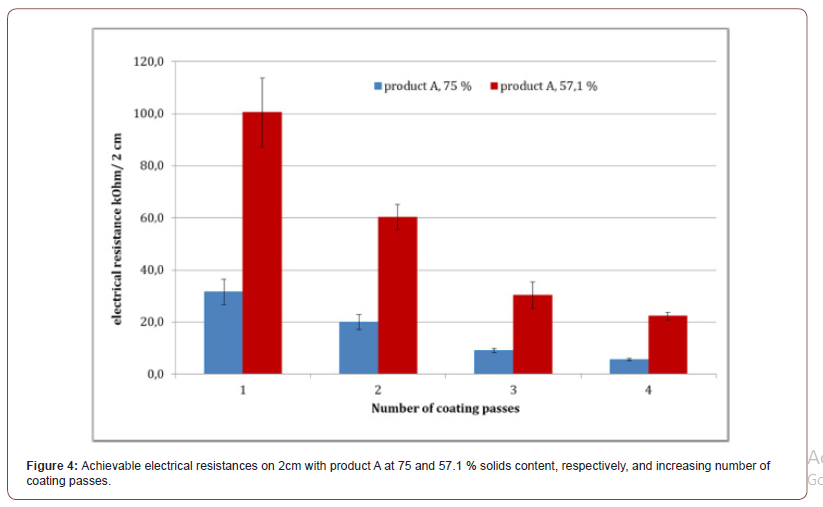
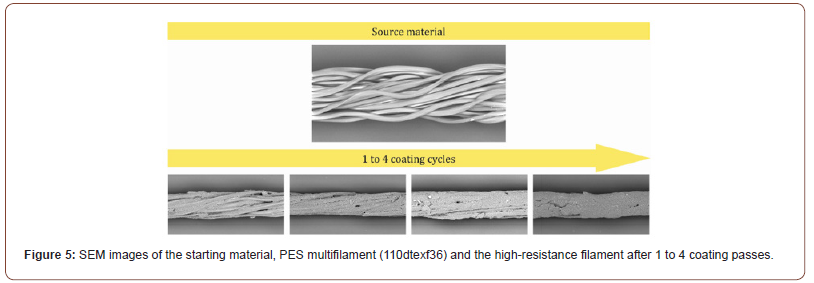
Processing, function and wash ability of the developed high-resistance yarns
The high-resistance yarns developed were processed further using textile technology on a narrow weaving machine to produce a heating tape that could be freely cut. This was followed by thermal fixing on the ironing press. The functionality of the conductor structure was verified by means of a thermal imaging camera. By applying different voltages of 12, 24 and 36 V to the heating tape, the change in current was also determined after different time intervals (1 and 3 min). At 12 V, the current does not change after 1 or 3 min. As the voltage increases, the current and the heating temperature increase.
In order to assess the chemical, thermal and mechanical resistance, washing tests were carried out on ready-made heating tapes made from the high-resistance thread in accordance with DIN EN ISO 6330 under the following conditions:
• 30 °C
• Air drying
• 10 washing cycles
• Specimen size 10 cm
• Number: 3 samples per variant
The electrical resistance of the heating surface decreases by approx. 67 % after the 1st wash. After the following washes, the electrical resistance of the heating surface no longer changes significantly, see Figure 6.
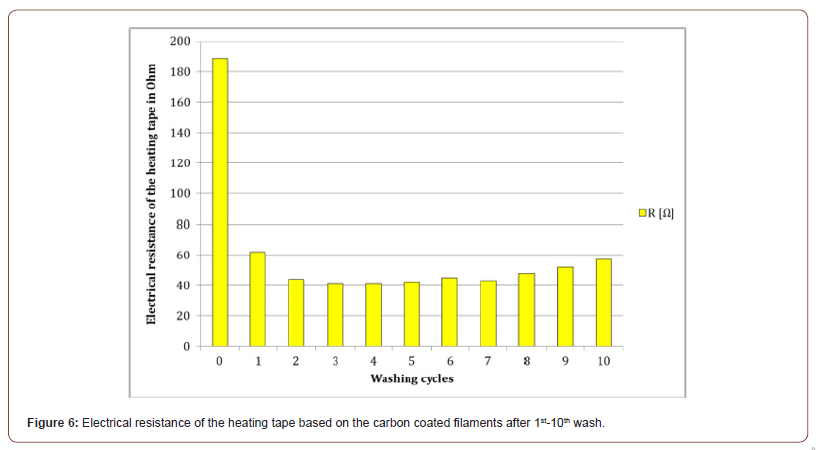
The thermal images in Figure 7 show that even after the 10th wash there is a uniform heat distribution in the heating tape. The stress in the washing process does not lead to any failure of segments of the heating tape. Moreover, the heating power increases after washing due to lower electrical resistance, which allows high current flow at the same voltage.
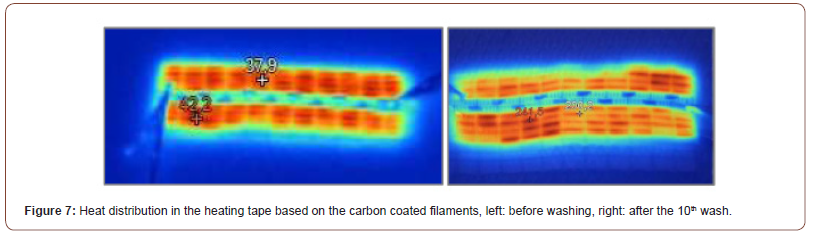
Optical microscopic images of the high-ohm resistance yarns in the fabric show the changes caused by the mechanical, thermal and chemical stress in the washing process. The conductive yarns based on the carbon coating show only minor changes in surface properties (Figure 8). After the 10th wash, only 3 individual filaments without coating are visible, which is why the adhesion of the carbon coating can be described as good. As shown in Figure 6, even the electrical resistances of the heating tapes decrease. It is therefore assumed that superfluous carbon-containing coating components are washed off and thus the current can flow better.
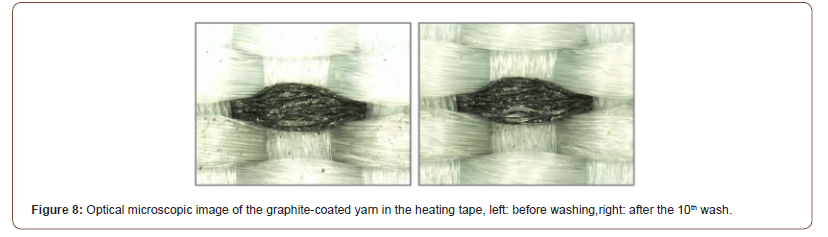
Adhesion improvement on monofilaments
To obtain homogeneous and adhesive conductive layers on PES monofilaments, a SiOx nanolayer is deposited in the first step by means of the combustion chemical vapor deposition (C- CVD), as shown in Figure 9. The characterization of the nanolayer formation is carried out by means of scanning electron microscopy (SEM) and energy dispersive X-ray spectroscopy (EDX). Figure 10 show an example of a nanolayer on a PES monofilament with a diameter of 0.170 mm, in which 1.15 % of silicon content has been detected.
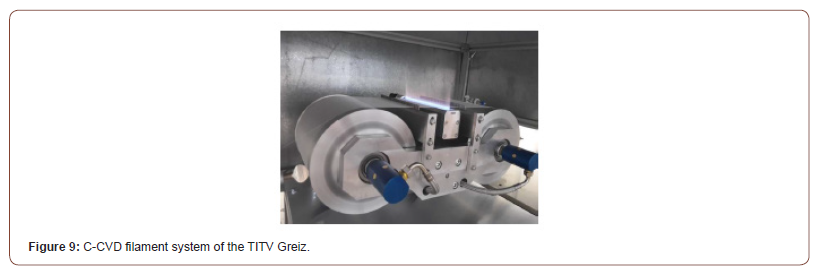
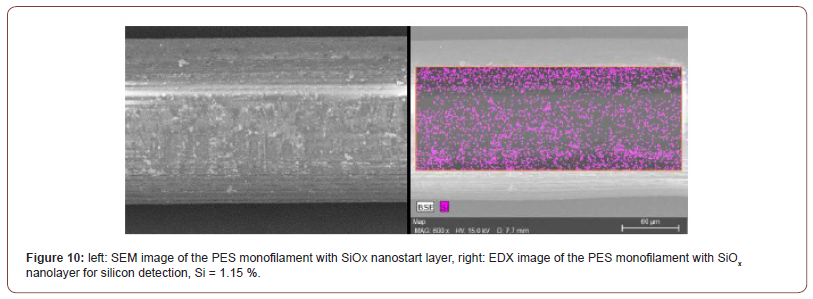
The conductive polymer coating subsequently applied by godet technique is chemically bonded to the SiOx nanolayer on the filament surface.
After one coating pass of the carbonaceous polymer coating, a lower electrical resistance is achieved on the C-CVD pre-treated PES monofilament than on a PES monofilament without C-CVD pre-treatment. This relative difference in the electrical resistance reduces with increasing number of the coating passes and is finally negligible, Figure 11.
Figure 12 shows that the coating formation is more uneven without the upstream C-CVD treatment. In addition, the carbon coating without the C-CVD treatment comes off even with slight friction by hand. With C-CVD treatment, the adhesion of the carbon coating is significantly improved, so that it cannot be easily detached, see Figure 13.
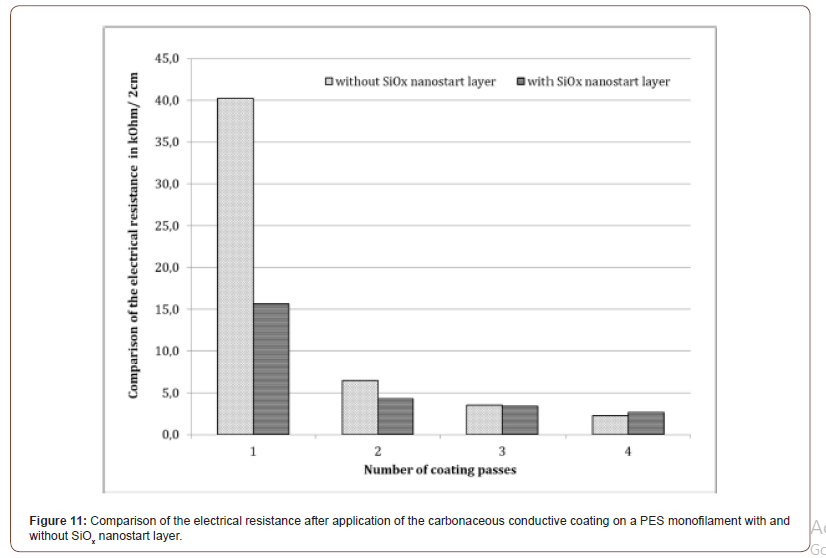
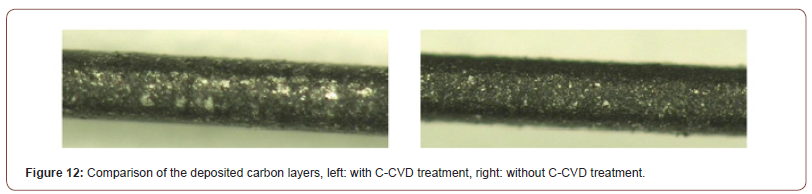
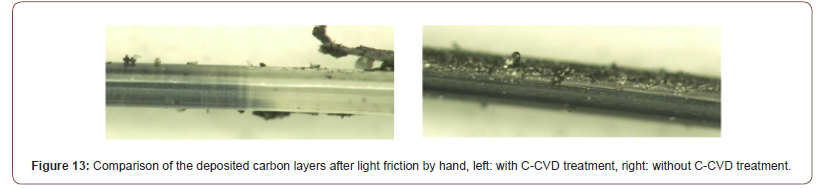
Conclusion
With the developed technology, defined and stable electrical thread resistances in the high-ohm range of 1-1000 kΩ/ m based on polyester multi- and monofilaments can be achieved over the filament length. This technology for generating conductive layers is transferable to any yarn material. The modification on the yarn surface to achieve the high-resistance properties is independent of the fibre material of the base yarn. The target electrical parameters are achieved by the conductive particles as well as the thermal modification of the coated polymer layer, thus a high-resistance yarn can be produced with any yarn material. The technology is based on the developed polymer coatings with conductive additives, which are applied via yarn coating processes, particularly the godet coating method. Homogeneous conductivity is achieved by means of adapted coating pastes and process parameters, thermal activation, but above all by multiple coating passes. The achieved range of variation in the electrical characteristics of < 10 % on 2cm yarn sections allows the use of the high-resistance yarn in freely cut textile heating surfaces. Sensor technology and shielding are targeted as further areas of application for the conductive thread developed.
The technology is currently being transferred to production scale for a standard product, taking economic aspects into account. This standard product is to be offered under the name hiTEX. The starting material for the standard product is a polyester multifilament with a fineness of 110dtexf36. The conductive polymer coating is applied to this by means of godet deposition, thus achieving electrical resistances of 200-700 kΩ/ m.
To read more about this article....Open access Journal of Textile Science & Fashion Technology
Please follow the URL to access more information about this article
To know more about our Journals...Iris Publishers
No comments:
Post a Comment