Authored by Ayodele Akinterinwa*,
Abstract
Urea formaldehyde (UF) resins have found a lot of industrial applications mostly as binder in woodworks and coating. The resin is a low-cost product synthesized from urea and formaldehyde in a sequential addition (methylolation) and condensation (polymerization) reactions. The addition reaction generates methylol and urea derivatives that proceed into condensation reactions. The condensation reactions takes the resin from its initial fluid state through to the formation of a thermosetting film, however, this is companied by release of formaldehyde which may be hazardous to health. As briefly highlighted in this review, having a concise knowledge of the chemistry of these processes will be an easy guide towards a successful synthesis of UF resins with improved performance and environmental attributes.
Keywords: Formaldehyde; Methylol; Resin; Synthesis; Urea
Introduction
Urea formaldehyde (UF), also known as urea-methanal, are known since 1915, its commercial production since 1928, and today UF accounts for about 15% of the total thermoset resin production [1]. UF resins are colorless water-soluble resins that cure to a colorless, glossy and compact thermosetting polymer film [2-4]. They are synthesized from step-wise addition and condensation reactions of urea and formaldehyde, which can be carried out within a wide range of conditions that makes it possible to optimize some important properties of the resin such as; gel and dry time, brittleness, moisture absorption, hazardous formaldehyde emission, tack, spreadability etc. [5-8]. UF resins are the most important amino resins, and their outstanding relevance is due to low cost, high reactivity, solubility in water, fast curing, film clarity, non-flammability, compactness, good resistance to heat and electricity [2-4, 8,9]. UF resins in the pure, modified and incorporated forms have formed the bulk and/or base material in many applications. Owing to their fast curing to compact thermosetting films, UF resins have found early applications as adhesives [10]. This adhesive property has also established UF resins’ potentials as binders in wood works and functional coatings [9,11-13]. Chemically, UF resins are rich in reactive amine, amide, hydroxyl, and carbonyl groups which can set into an organized structure in the resin film. The potentials of these functional groups as chelating sites in the UF resin have been explored in some novel applications. A novel polychelate of metal ions with good antibacterial activities was synthesized using UF resin by Nishat et al., [14]. Low-cost UF microspheres have also been developed from UF and used in a high efficiency removal of heavy metals (Pb2+, Cd2+ and Cu2+) from wastewater [15].
Understanding the chemistry of UF resin is very important in its synthesis and applications to sustain economic and environmental friendly practices. Formaldehyde emission is the major environmental challenge with UF resins, while the resin’s rate and extent of curing (brittleness) and water uptake which may lead to early failure, are of economic concerns [2,16-19]. One of the strategies to reduce the formaldehyde emission of UF resins has been the change on its formulation by decreasing the molar ratio of formaldehyde to urea, although this will upset other effects. Therefore, it is necessary to optimize the synthesis of UF resins, by changing the production process [4-8]. This paper will focus on the basis of UF resins, and the knowledge from it will be an easy guide in understanding some basic factors that are critical in the production of UF resins.
Materials and Methods
Urea
Urea also referred to as carbamide (CO(NH2)2) is a natural product of protein metabolism found in urine from which it was first isolated. It was synthesized from ammonium cyanate in 1828 by Friedrich Wohler (Scheme 1 and Figure 1), and it was the first organic compound to be synthesized [20]. Urea is non-flammable, non-toxic, and colorless in its crystalline form, with a density of 1.32 g/cm3, melts at 132.7 °C and soluble in water, alcohol, and benzene. It is used in the production of fertilizers, plastic adhesives, flame-proof agents, and in medicine [21] (Scheme 1 & Figure 1).

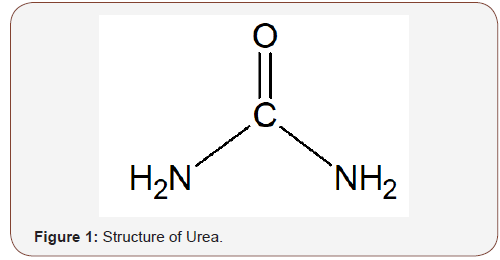
FormaldehydeFormaldehyde also referred to as methanal occurs naturally in certain foods such as coffee, dried bean curd, cod fish, caviar, maple syrup, shiitake mushrooms, smoked ham and it is also a natural metabolic product of the human body [22-24]. It was first synthesized by Alexander Butlerov in 1867 [25]. Industrially, formaldehyde is produced through the catalytic oxidation of methanol (Scheme 2). Formox process is a commonly used process in which the reaction is carried out at about 250–400 °C with mixture of iron oxide and molybdenum and/or vanadium [26]. However, other procedures aimed toward a sustainable production are now available [27]. Formaldehyde is a colourless gas at room temperature with a pungent irritating odour, and the simplest member of the aldehyde family with the molecular formula CH20 (Figure 2). It has a density of 0.82 g/cm3, melts at -92°C, boils at -21°C and soluble in water, alcohol, and many other polar solvents. It is usually stored and used as a 37-40% aqueous solution called “formalin” which contains 10–15% methyl alcohol added to inhibit polymerization. Formaldehyde has found a wide application especially in its use in the production of such valuable synthetic resins as; phenol formaldehyde, urea formaldehyde and melamine formaldehyde, and also as disinfectant and as preservative for biological species [17, 28].

The International Agency for Research on Cancer (IARC) [29] in 1987 and in 2006 has classified formaldehyde as a probable human carcinogen. The agency in 2006 also reported the various processes from which formaldehyde is released into the atmosphere and these includes; formaldehyde and its resins manufacturing plants, plywood and particle board mills, furniture factories and other wood product plants, paper and textile mills, garment factories, foundries, man-made mineral fiber plants, plastic production, and other miscellaneous processes such as photographic film manufacturing and development, emulsion paint resins, embalming funeral homes, and disinfecting in hospitals [29,30]. The National Industrial Chemicals Notification and Assessment Scheme [31] reported that formaldehyde levels between 0.1 and 0.5 ppm are detectable by human senses, between 0.5 and 1.0 ppm can cause eye irritation, and above 1.0 ppm can irritate the nose and throat. The World Health Organization has however recommended an indoor limit of about 0.08 ppm [32]. In general, formaldehyde is an important chemical for the global economy, but a high-dose exposure increases the risk of acute poisoning, while prolonged exposure can lead to chronic toxicity and cancer [22,33] (Scheme 2 & Figure 2).

Results and Discussion
Urea formaldehyde
UF is synthesized from urea and formaldehyde. The addition reaction (scheme 3) is an endothermic reaction that results in methylolation or hydroxymethylation of urea (Scheme 3). The addition reaction starts with the deprotonation (abstraction of hydrogen atom) of urea by formaldehyde to form the electrophilic methylol (-CH2OH), which is bonded back on the deprotonated site(s) on the nitrogen group of the urea to form the methylol urea derivatives. There are four possible deprotonation sites on urea; therefore a maximum of four molecules of formaldehyde can react Citation: Ayodele A, Abdullahi I, Benson A. Concise Chemistry of Urea Formaldehyde Resins and Formaldehyde Emission. Insi in Org & Inorg. 1(2): 2020. IOIC. MS.ID.000507. Insights in Organic & Inorganic Chemistry Volume 1-Issue 2 Page 3 of 6 with a urea molecule). pH, stoichiometry (i.e. Formaldehyde: urea ratio), types and amount of catalyst, temperature, types and amount of modifiers, reagent quality/assay and reaction time are among the parameters that may affect the synthesis of UF [34,35]. Practically, UF resins synthesized under favorable conditions is a mixture of methylol derivatives and methylenediurea (Scheme 3) [36,37]. Trimethylol is the most favorable synthesized derivative, dimethylol have been synthesized in highly alkaline medium, monomethylol is reversible, while tetramethylol is thermodynamically unfavorable [8,38,39]. As the reaction proceeds, deprotonation of urea cause the pH to gradually drop towards acidity, thereby making the reaction unfavorable with time. The presence of some catalyst may therefore be required in the synthesis of UF to serve as a buffer. Examples of such catalysts are; ammonia, ammonium hydroxide and sodium dihydrogen phosphate.
Temperature is another critical factor in the addition reaction step of UF. The endothermic reaction will only start when enough energy is supplied at elevated temperatures. At appropriate temperatures above the threshold limit of the reaction, urea is dissolved in formaldehyde to form a clear solution in which the addition reaction is expected to be initiated. However, any sudden drop in temperature or pH may hinder the initiation of the reaction, causing urea to precipitate as a sign of failure of the addition reaction and hence the synthesis of the resin. Low grade or contaminated reagents (especially formaldehyde) may also cause the precipitation of urea in the addition reaction stage (Scheme 3).
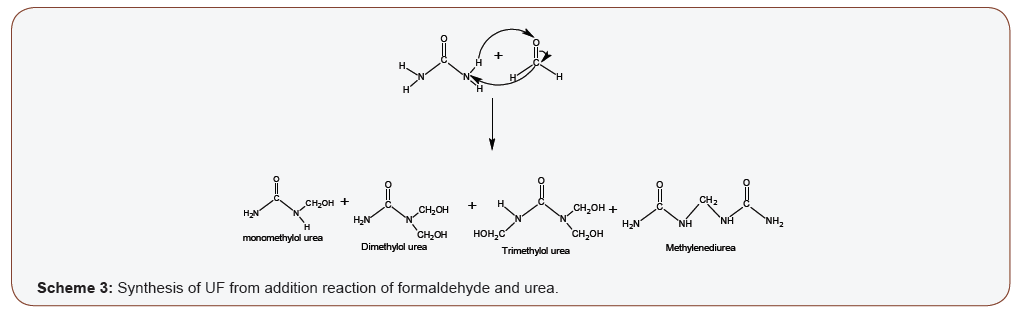

Condensation reaction follows the addition reaction and it occurs between methylol and urea derivatives and even among the methylol derivatives in the resin to form unstable methylene (-N-CH2-N-) and dimethylene-ether (N-CH2-O-CH2-N) linkages, as shown in Scheme 4. Condensation is a polymerization reaction; hence it results in the formation of the polymeric structure in UF resins in which the methylol and urea derivatives link in different fashions resulting in chain growth and crosslinking. During the condensation reactions, the viscosity of the resin increases slowly and the rate increases to be very rapid after a critical time [37]. It can also be regarded as the onset of the curing process [40]. Condensation reaction is more favorable in acidic medium; hence it proceeds faster at low pH. This is because; the removal of OH groups on methylol urea derivatives is more favorable in acidic medium. The different pH region required for a favorable addition and condensation reactions serves as the basis for the common two-step process used in the synthesis of UF resins. In the two-step process, the pH of the reaction is reduced (to be acidic) after a predetermined time in which the addition reaction is deemed to have reached an optimum stage. The reduction in pH is to favor the initiation of condensation reactions, and the rate of the condensation reactions increases as the pH of the reaction is decreased. Different rate of condensation may be required in UF resins for different applications. In applications where fast curing is required (e.g. woodworks), rapid condensation reactions will be required in UF resin, and this have been achieved with the twostep process. However, for applications in which a slower curing UF resin is required, such as coatings, a one-step process carried out at intermediate pH was reported by Barminas and Osemeahon [41,42]. In other reports, methods have been used to enhance the rate of condensation/curing as well as the structure of the cured resin films to optimize the performance of UF resins [39,43] (Scheme 4).
Condensation reactions take the UF resin through the stage of methylol and urea derivatives in fluid form to high molecular weight polymer molecules with 3D cross-linked networks in gel form (Figure 3), and finally to the insoluble thermoset film. This phenomenon is refered to as curing. The chemical structure of UF resins can be specified as poly (methylene methylene ether hydroxymethylureas). This however leaves the details of the structure undetermined, as there are mixtures of different linear and mostly branched macromolecules characterized by the average molar mass (or molar mass between branches) and the content of different functional groups [44]. The wide range of molar mass distributions in UF resins (i.e. the presence of various molecular species from low molar mass to large polymer molecules) presents various chemical characteristic while influencing several important properties of the resin, such as: viscosity, flow-ability, penetration into the wood surface, water dilute ability etc. The highest molar masses in UF resin cannot be clearly determined, but it is estimated that molar masses of 100000 to 500000 g mol–1 can successfully describe the structure of UF resins [45] (Figure 3).

The two basic challenges with UF resin applications are formaldehyde emission and moisture uptake. The processes involved in these challenging phenomenon starts from the condensation reactions during the synthesis of the UF resin and may last throughout the lifetime of the cured UF film. However, many works have been done to successfully reduce formaldehyde emission and improve water/moisture resistance of UF resins [4,46-50].
Formaldehyde emission
As condensation continues, methylene linkages which are more stable are formed, and the process is accompanied by the release of formaldehyde (Scheme 4c and d). Also, the polycondensation of UF resins to cure into film is reversible. In the forward reaction, water is eliminated; therefore, the reverse reactions can be viewed as hydrolysis (Scheme 5). Atmospheric moisture is the constant source of the water molecules involved in this reverse hydrolysis. The methylol derivatives from the reverse hydrolysis reactions will apso interact to release formaldehyde (Scheme 4c and d) [51- 53]. In addition to formaldehyde emission, the reverse hydrolysis reactions degrade the structural integrity of the UF film which may lead to its failure in stress-bearing applications. Therefore, the more UF films are exposed humidity, the faster the rate/extent of degradation, and this is why UF-bonded products are normally confined to interior, non-structural applications in building [2,54] (Scheme 5).

Conclusion
Most times, failures encountered during the synthesis and application of UF resins are due to inadequate knowledge, confusing or ambiguous information about the details of the processes involved. In this report, the reaction of urea and formaldehyde to produce UF resins have been discussed with simple and clear terms. pH is a critical factor in the processes. The addition reaction is sensitive to some reaction conditions (e.g. pH, temperature and impurities), and when this step fail, the process cannot proceed, hence the whole synthesis is failed. Condensation reactions increase the molecular weight and molecular weight distribution of FU resins. Condensation reaction proceeds till the resin are completely cured, and the rate of condensation which is directly proportional to the rate of cure can be optimized from the UF synthesis procedures. Formaldehyde molecules are released during condensation reactions as well as the reverse hydrolysis reactions by water or atmospheric moisture. The later can also form part of the degradation process of the UF resins. This review will be a quick guild to acquire knowledge of the basic chemistry and chemical process involved in the synthesis and application of UF resins.
To read more about this article....Open access Journal of Chemistry and Biochemistry
Please follow the URL to access more information about this article
https://irispublishers.com/icbc/fulltext/concise-chemistry-of-urea-formaldehyde-resins.ID.000507.php
To know more about our Journals...Iris Publishers
No comments:
Post a Comment