Authored by Lucy Feleke Nigussie*,
Abstract
Construction industry in Ethiopia is growing fast due to rapid urbanization and accommodation demand for affordable housing for residents. This activity generates a large amount of construction and demolition wastes, which are commonly disposed of as landfill and cause environmental and economic impacts. Recycling construction and demolishing waste is one of the viable solutions to reduce environmental pollutions and makes construction sustainable by lowering the dependence on natural and non-renewable resources. In this study, the effect of recycled fine aggregate from the demolished hollow concrete block on the workability, density, and compressive strength of concrete was studied. A comparative analysis of the experimental results of fresh and hardened concrete properties with different replacement ratios of natural river sand by recycled fine aggregate is presented in the paper. Concrete mixes containing 25 %, 50 %, 75 %, and 100 % replacement of natural sand with the recycled fine aggregate were tested. The test results indicated have lower physical properties than the control, but they have satisfied the ASTM requirements. The replacement of natural river sand by recycled hollow concrete block slightly affected the workability, density, and compressive strength of the concrete. The performance of the concrete containing recycled fine aggregate decreased with an increase in the percentage of replacement of fine aggregate increased, and the targeted compressive strength was met up to 50 % replacement Therefore, this work demonstrated that the suitability of using demolished hollow concrete block as fine aggregate, and this could reduce the environmental impact due to waste disposal and sand mining.
Keywords:Compressive strength; Concrete; Demolition hollow concrete blocks; Recycled fine aggregate
Introduction
As a result of a change in the living standards and an accelerated rate of urbanization, the construction industry is booming globally. The construction industry is among the most prosperous economic sectors around the world as it transforms various resources into the constructed infrastructure necessary for socio-economic development. Despite the relevance to the socio-economic growth, it’s also recognized that construction activities and the natural environment are interconnected [1]. Lately, waste generation due to demolition has become an essential issue with possible negative impacts on the environment. There is a large amount of construction and demolition (C&D) waste generation due to: new zoning bylaws, modified settlement patterns, increased population in urban areas due to industrial development, modernization of old road, and bridges for the present as well as for future growing traffic, and during renovation and demolition of existing building [2].
Ethiopia is experiencing problems, of rapid population growth rate, lack of education amongst the population, uncontrolled rapid urbanization, affordable housing shortages, and erosion. Along with most of the African cities, Ethiopian cities don’t have the spatial, physical, and socio-economic requirements fundamental to sustain the livelihood of the city. To address the problems, the Ethiopian government has been implementing transformation plans and low – cost housing programs [3,4]. These programs were launched during different phases according to the agreements reached such as the Sustainable Development and Poverty Reduction Program (SDPRP) from 2002-2005, and the Plan for Accelerated and Sustained Development to End Poverty (PASDEP) from 2005-2010. In every program, the government planned to construct affordable houses for the citizens. From 2004-2008, the programs planned to build 150,000-200,000 housing units [5]. Such construction programs require demolition of existing buildings, which will generate a huge amount of wastes.
The major problem the construction industry facing is the disposal of C&D wastes. C&D wastes are directly dumped as a landfill, causing environmental pollutions. Demolition wastes comprise a large fraction of waste dumped as landfills worldwide, both in developing and developed countries. For example, in Australia 7.7 million tons of waste gets disposed of as landfills annually [6]. These demolition wastes consist of inert and non-biodegradable materials, such as concrete, metals, bricks, glass, finishing material like tiles, paintings, gypsum, as well as electrical and sanitary fittings, and fixtures, in different size and amount [7,8]. These inert and non-biodegradable wastes will remain in the environment for thousands of years as well as affect the environment by claiming large landfill areas, which can lead to disposal land depletion. In developed countries, there is a restriction by law on construction and demolition wastes in the form of prohibition, or by creating special taxes for creating waste areas [9,10]. But, in Ethiopia, C&D waste management is undertaken by urban administrations, or they may agree with construction enterprises to dispose of solid waste as backfill to quarry pits [11]. Although it’s possible in many countries to estimate the amount of demolitions waste expected from a given site, this is not yet a common practice in Ethiopia. For example, in the European Union (EU), about 850 million tons of construction and demolition wastes are generated annually [12], but no record was available for the amount of C&D wastes in Ethiopia due to lack of tracking the solid waste disposal.
The C&D waste must be reduced by using the waste for a different purpose through the waste hierarchy, which aims to reduce, reuse, or recycle waste [13]. Recycling and reusing of the C&D wastes may minimize the extraction of non- renewable natural resources. The importance of recycling demolition material has been raised due to the scarcity of natural sand, the large volume of landfills, extraction of riverbeds as well as other environmental concerns. Sand is mined worldwide in a large volume next to water, and it accounts for 70-80% of the 50 billion tons of materials mined per year [14]. Recycling has many benefits that have made it a more attractive option in conserving non-recyclable natural resources, in creating environmental awareness to reduce the impact of a landfill, as well as reduce the disposal cost which can lower construction costs [15,16]. In Ethiopia, the concept of recycling C&D waste is not yet put into practice [17]. The current practice in Ethiopia is disposing of these demolition wastes as landfill as per solid waste management proclamation No. 513/2007 of Ethiopia [18].
The type and amount of waste generated will vary from country to country and from place to place. In Ethiopia, there is no research done on the characterization of the waste types generated from demolition activities. But it is possible to know which materials were abundantly used in the construction is not industry. In Ethiopian, the use of concrete for the structural part and hollow concrete block (HCB) for walls is a common construction practice. The popular material for walls, whether an internal or external wall, is HCB [19]. The demolition wastes in Ethiopia contain a large amount of demolished HCB that goes to landfill. This needs to be recycled to be used in concrete productions to reduce the environmental impact due to waste disposal and sand mining.
The objective of this study is 1st to examine the capability of recycling demolished hollow concrete block wastes for production of new concrete by characterizing the physical properties of recycled fine aggregate (RFA), 2nd investigate the effect of replacement of recycled fine aggregate in the production of concrete and 3rd determining the optimum replacement percentage of river sand by recycled fine aggregate. The test was checked as per ASTM standard requirements. Ethiopia uses ASTM and ACI standard specification through amendment and modification to satisfy local requirements in local technology.
Literature Review
Generation of the enormous amount of C&D wastes as well as depletion of natural sand enforces for utilization of the C&D wastes as aggregate in an effective manner by recycling or reusing crushed concrete with aggregate. Recycling of demolition debris was started since the end of 2nd world war, which used crushed brick as aggregates in concrete [20]. Using crushed concrete from demolition waste as aggregate instead of natural resources as well as using demolished concrete pavement to stabilize the road base courses during past decades has been recognized as a most practical and sustainable way of C&D waste handling methods. But most recently various researchers found that how demolished concrete wastes can be used in concrete as structural rather than the base course of roads. Umoh [21] examined the use of demolition waste sand Crete blocks as aggregate in concrete. The finding was, crushed waste sand Crete block can be used as supplementary aggregate materials in concrete. Ashraf et al. [9] examined the recycling of construction and demolition concrete waste as aggregate for structural concrete. They claimed that the replacement of 25% recycled concrete aggregate has no significant adverse effect on structural concrete performance. When the replacement ratio increased to 50%, the compressive strength reduction ranged from 7% to 13%. Özalp et al. [22] investigated the effect of recycled aggregates from construction and demolition wastes on mechanical and permeability properties for manufacturing of different concrete products like concrete paving stone, kerb, and concrete pipes. The researchers concluded that with appropriate separation and classification, using recycled concrete aggregate as a secondary raw material in various concrete elements is possible with the related standard. Shehata et al. [23] evaluated the properties of recycled concrete aggregate (RCA) of preserved quality, which was produced through the way that preserves the original properties of the concrete to be recycled. The study showed that concrete with RCA of preserved quality performed significantly better in compressive strength, drying shrinkage, and salt scaling resistance. Martinelli et al. [24] investigated the feasibility of alternative processing procedures to remove impurities of recycled concrete aggregate. The research also examined their influence on the physical and mechanical properties of the aggregate and the concrete mixes. They claimed that the autogenous cleaning procedure significantly reduced the gap between the performance of the recycled concrete aggregate and the natural aggregate by removing surface impurities and reduce particle heterogeneities. This reduction of impurities enhances the properties of concrete with recycled aggregate at fresh and hardened state. Woubishet [17,25,26] investigated the suitability of recycled concrete aggregate in concrete and the effect of recycled concrete aggregate on concrete properties. The researcher concluded that the recycled concrete aggregate has lower physical and mechanical properties than natural concrete aggregate but in the range of normal weight aggregate. Generally, the study comes with the suitability of recycled concrete aggregate in the production of new concrete in Ethiopia.
From the studies above, recycling demolished, and construction wastes as concrete aggregate for concrete products were investigated to a significant level. Unlike in Ethiopia, the recycling of C&D waste concept developed to the extent of enhancing the performance of recycled concrete aggregate to remove the impurities and using for structural elements. Ethiopia is one of the developing countries in Africa and using these researches in developing countries like Ethiopia is impossible due to technology transfer gap between developed and developing countries. Only a few studies were carried out on recycling C&D wastes as concrete aggregate in Ethiopia in local techniques [17,25,26]. The previous researchers in Ethiopia investigated on the demolished concrete structure to recycled concrete aggregate but not addressed hollow concrete blocks, which is most abundantly available wastes.
Materials used and Experimental Procedure
Materials used
In the material selection and quality assurance, the Ethiopian technical specification [27] elaborated which standard to be used and means of measurement.
• Cement: Dangote Ordinary Portland cement with a grade of 42.5R (CEM I) was used. The physical properties of the cement are shown in Table 1.
Table 1: Rate of all types of weather crashes.

• Coarse aggregate:Coarse limestone aggregate with a maximum aggregate size of 20 mm was used.
• River sand: Locally available river sand from Chewaka was used in the mix.
• Water: Potable tap water was used for concrete mix and curing. No chemical admixtures were employed in the mixes.
• Recycled fine aggregate: The recycled fine aggregate from demolished HCB was used as a replacement for river sand. The demolished HCBs were collected from demolished buildings in Jimma University main campus, which were used as a student dormitory. The external and internal walls of the demolished buildings were constructed using HCBs before ten years. In recycling the demolished HCB for fine aggregates, the following techniques were used: sorting the demolished HCB from disposal sites, removing unnecessary attachments on HCB like ceramics from toilet and shower rooms, crushing the blocks by rock hammer to the desired sizes to fit into the crushing machine and then crushed into different sizes. Grading of the crushed aggregates was done using standard sieve analysis, and the recycled aggregates passing sieve size 4.75mm were characterized as fine aggregates. The RFA has several impurities like gypsum, clay, wood, ceramic, and organic materials. These impurities were eliminated by screening, handpicking, and washing RFA.
Properties of materials
The properties of materials were tested as per ASTM standard procedures. The properties of cement summarized in Table 1 below. The fineness of the cement affects the hydration rate. The fine cement reacts faster with water, and the rate of strength development is also high. The fineness of the OPC was tested as per ASTM C 184 [28], and for OPC, the percentage of residue retained after sieving by No. 200 sieve should not exceed 10% by weight. From Table 1 the fineness of cement is within the required limit. The setting time of the OPC 42.5R was checked as per ASTM C 191 [29], and the initial setting shall not be less than 30 min and for final setting time not greater than 600min which satisfied the requirements. The normal consistency property of OPC was tested to determine the optimum amount of mixing water as per ASTM C 187 [30].
The properties of RFA and river sand were summarized in Table 2. The maximum silt content of fine aggregate for all concrete types as per ASTM C 33 is 6% [31] if the silt content exceeds 6%, the sand has to be washed before use. The silt content of river sand (2.87%) being less than the above limit, there was no need to wash the sand.
Table 2: Summary of properties of RFA and river sand.
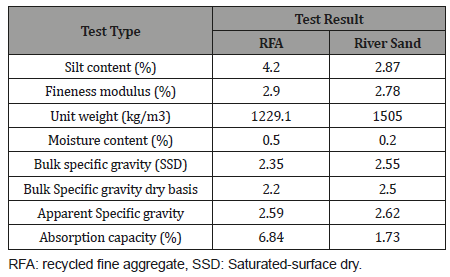
The silt content of RFA from the demolished hollow concrete blocks was done after sieved as per ASTM C 117-90 [32]. The fine particles which pass 75μm in the RFA are more than the limit (6%), which is 14.2%. This is due to cement powder from mortar and dust of fracture during the crushing process. Therefore, the RFA has to be washed so that these fine particles will get reduced. After washing measurements showed that silt content is reduced to 4.2%, which is less than 6% and within a desirable level of use. As silt content increase the stiffness of the specimen increased due to dry unit weight and density increment [33].
The unit weight of the RFA was less than that of river sand, and this was attributed to the porous cement mortar adhered to the RFA. The unit weight of both river sand and RFA is within the acceptable range of ASTM standard [34]. The density less than 1120kg/m3 is called lightweight and RFA was not in this range, which is greater than 1120kg/m3.
The water absorption capacity of fine aggregates has to be within the range of 0.2 to 2% and on Table 2 the result of river sand is within the range which satisfies the requirement. The water absorption capacity of the RFA is higher than the range specified [16]. This high-water absorption capacity (6.84%) is due to the fine particles and adhered mortar.
The bulk density of recycled aggregate is less than that of natural river sand, and the same phenomena existed with former researchers [21]. The reason is the presence of mortar adhered to the natural sand and fine particle from the mortar. The moisture content of recycled fine aggregate from the demolished waste of hollow concrete block is taken after washed, and due to this, the moisture content is higher than that of river sand. As per ASTM C 33 [31] requirement, all properties listed in the table above are within the range (Table 2).
As per Figure 1 the gradation curve of river sand and RFA lays between upper and lower limit, which satisfy the ASTM standard requirement. The fineness modulus of both river sand (2.78) and RFA (2.9) lays in the range of 2.6-2.9, which is a medium sand type (Figure 1).
center>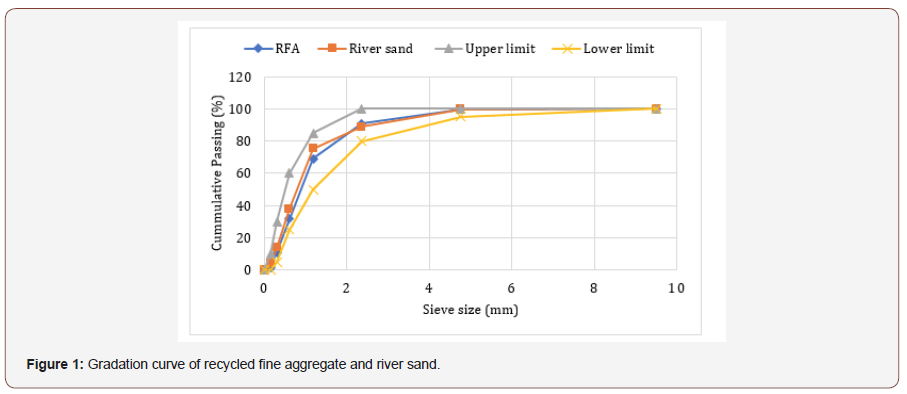
Finite Element Model
The unit weight of coarse aggregate is within the range of 1200-1760kg/m3, and it fulfills the ASTM requirement. As per ASTM C 33, bulk specific gravity at SSD of coarse aggregate have to be within the range of 2.4 to 3.0, and the aggregate is satisfied the requirement. The absorption capacity for coarse aggregate has to be from 0.2% to 4% and in Table 3 below the absorption capacity of coarse aggregate satisfy the requirement of ASTM C 33.
It can be observed that from Figure 2 the gradation curve of coarse aggregate is between the upper limit and lower limit, which show that the coarse aggregate is well graded.

Experimental procedures
The effect of recycled fine HCB aggregate on the compressive strength of concrete was studied. The mix design was done to achieve a compressive strength of 25 MPa with different percentage of replacement of river sand with RFA. This is the comparative study of control mix with different percent replacement of demolished recycled fine aggregate. The following properties of the materials were tested.
• Cement: Fineness, setting time, normal consistency
• Coarse aggregate: Silt content, gradation, density, specific gravity, and water absorption
• River sand: Silt content, gradation, density, specific gravity, and water absorption
• Recycled fine aggregate: Silt content, gradation, density, specific gravity, and water absorption were tested as per ASTM standard.
Mix design
Characteristic compressive strength (fck) 20 MPa, which is C-25 [35] Normal strength concrete
Choice of slump set to be 25 - 50 mm (minimum slump possible) Maximum aggregate size - 20 mm.
Mixing water requirement - 185kg/m3 as per ACI Table 3. 8 for the slump range 25- 50mm
Table 3: Summary of properties of coarse aggregate.
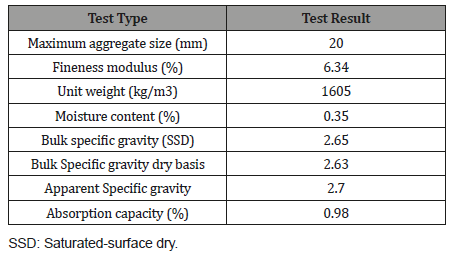
Water to cement ratio - 0.5
Cement content - 370Kg =185/0.5.
Coarse aggregate content - 995.1 kg/m3 of coarse aggregates
Fine aggregate content - 805kg/m3
Water after adjustment - 204kg/m3
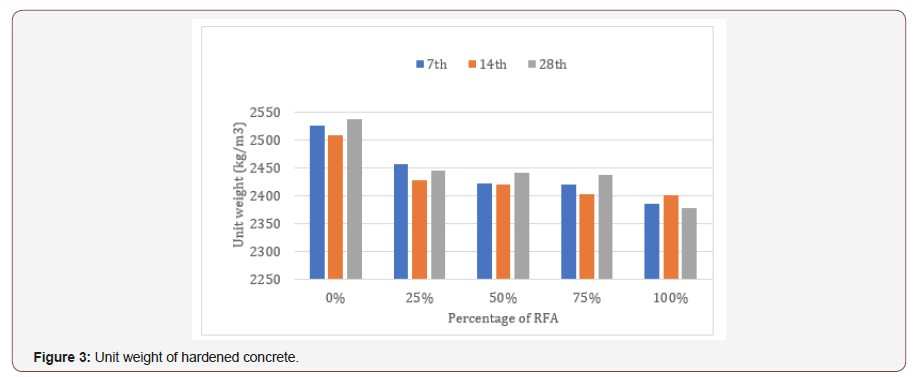
The concrete mix was performed based on weight proportions and prepared by replacing river sand by recycled fine aggregate with 0%, 25%, 50%, 75%, and 100% by mass. The mixes were designed for C-25 MPa as per ACI 301 for 28-day compressive strength [35]. The compressive strength of concrete is determined from tests on 150mm cubes at the age of 28 days in accordance with Ethiopian Standards [36]. In Ethiopia the commonly used concrete grade for the structural part is C-25 There are five types of mix with the coding of C, RFA25, RFA50, RFA75 and RFA100 which represent control (0%), 25 %, 50 %, 75 % and 100 % replacement percentage of river sand by RFA respectively (Figure 3). The nonair entrained concrete with the consistent placement of minimum slump (25mm-50mm) is selected. For the mixes, the properties of fresh concrete as per ASTM C 143 for slump test, the settlement of concrete from molded truncated cone shape was measured [37]. The compressive strength at the age of 28days frequently used as a parameter for structural design [38]. For compressive strength test, the concrete specimen was cast in a 150mm*150mm*150mm cube steel mold, and the tests were performed at 7, 14 and 28 curing periods. The specimens were demolded after 24hrs of casting and placed in a water bath. The specimens were cured at the room temperature (23 °C) in a water bath until tested. These experiment tests were undertaken in December 2018 in Jimma University Construction laboratory. The density of concrete was measured before the compressive strength test. During the testing of compressive strength, a calibrated compression machine with a uniform rate of 5 N/mm2 per second loading was maintained, and the maximum load to failure at which the specimen breaks and the pointer start moving back was noted (Table 4).
Table 4: The mix composition of concrete cubes.

Results and Discussions
Fresh concrete properties
Workability test:Slump test was performed to test the workability of fresh mix concrete as per ASTM C 143 [37]. The test was done for all different concrete mixes, including the control mix. Slump value of concrete with recycled fine aggregate was below the minimum (25mm) which is 12mm for 25% replacement, 9mm for 50% replacement. The lesser slump value than the control mix is due to the high-water absorption capacity of RFA. This high absorption capacity is due to the fine particles in the recycled fine aggregate, which results from the old mortar in it. The amount of these fine particles was reduced through washing and sieving by 150micro sieve. Adjusting for moisture and absorption capacity of recycled fine aggregate enables to attain uniform workability of concrete. The workability of the mixes was consistent since the water required for the RFA was adjusted during mixing. The other researcher concluded that [39] the workability of the concrete with natural river sand and RFA is almost the same if the saturated surface dry recycled aggregate is used. And also, if the dried aggregate is used and the amount of water required is added while mixing the same workability of concrete can be achieved.
Water-cement ratio:As shown in Table 5 the water-cement ratio varies for each percentage of replacement of the recycled fine aggregate. Due to the absorption capacity of the recycled fine aggregate, the amount of water required increase as the percentage of replacement increases. The gradual increment of the watercement ratio is to maintain the same workability range of concrete with recycled aggregate. The water-cement ratio ranges from 0.55 to 0.65. The water to cement ratio was varied to balance the water demand in a mix due to the high absorption capacity of RFA to maintain the same workability. In the previous study, adding the same amount of water required for the absorption of RFA to the mix during mixing or using saturated surface dried recycled aggregate can have the same workability [39]. In this study, the water to cement ratio varies from 0.55 to 0.65 due to adjustment required for the absorption capacity of the RFA.
Table 5: Summary of properties of coarse aggregate.
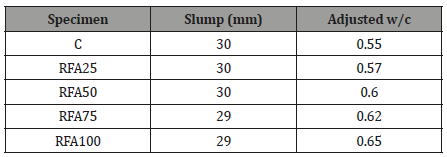
Properties of hardened concrete
Unit weight of hardened concrete:The unit weight of hardened concrete with recycled fine aggregate with different percentage was compared to the control specimen. There was a slight decrement of unit weight of hardened concrete as a percentage of replacement of recycled fine aggregate increased [22]. This decrement was due to the less density of the RFA. The research on physical and mechanical properties of recycled aggregate from construction demolition wastes in concrete [40] concluded that the recycled concrete aggregate density is less than that of the natural aggregate due to porosity which causes the lightweight concrete and this result was due to the density of recycled aggregate (Figure 3).
Compressive strength:Compressive strength of concrete at the age of 7th, 14th day, and 28th day curing periods are given in Figure 4. The concrete gain 65 % of its compressive strength on the 7th day, 90% on the 14th day, and 99% on the 28th day of curing. The compressive strength decreased as the percentage of replacement of recycled fine aggregate increased [41]. But the replacement of recycled fine aggregate up to 50% attained the mean target strength. The 28th average compressive strength of the control specimen is 37.50 N/mm2. The compressive strength of concrete specimen with recycled fine aggregate with percentage replacement of 25%, 50%, 75%, 100% is 32.10 N/mm2, 31.19 N/mm2, 27.25 N/ mm2, and 26.86 N/mm2 respectively. The compressive strength result obtained for RFA replacement percentage of 25% and 50% was above 99% of the targeted mean strength on 28th days of curing periods. But the replacement above 50% RFA has a lower result than mean targeted strength. The compressive strength of concrete specimen with RFA of 25%, the replacement had 16.82% reduction from the control mix, and the 50 % RFA replacement had 20.24% reduction from the control mix. The compressive strength decreased with percentage replacement of recycled fine aggregate due to the waste from painting, gypsum, and fine particles from old cement. The investigation on the suitability of recycled concrete aggregate in concrete production in Ethiopia [17] concluded that the compressive strength of C-25 concrete with recycled concrete aggregate is diminished by 17% and 9% at the age of 7 and 28 days respectively as compared to the reference mix but attained the targeted mean strength (Figure 4).
The compressive strength test result is the average of three samples for each percentage and each curing period. This replication is for accuracy and consistency of the consecutive results. The Figures 5,6&7 shows the relationship between the compressive strength and the percentage of replacement of RFA on 7th, 14th and 28th day of curing periods. As the coefficient of determination (R2-value) getting closer to 1, it indicates the degree of accuracy of the determined slopes and the R2-value on Figure 5,6&7 ranges from 0.904 to 0.9819. That is, the properties of the concrete have consistency throughout the test of different percentage replacement.
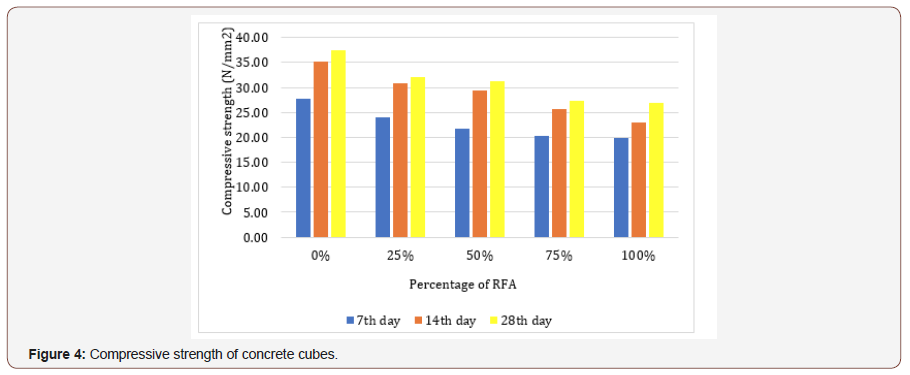
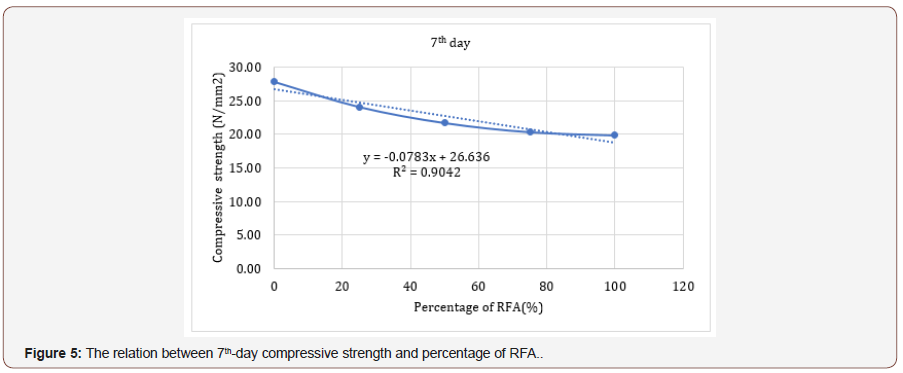
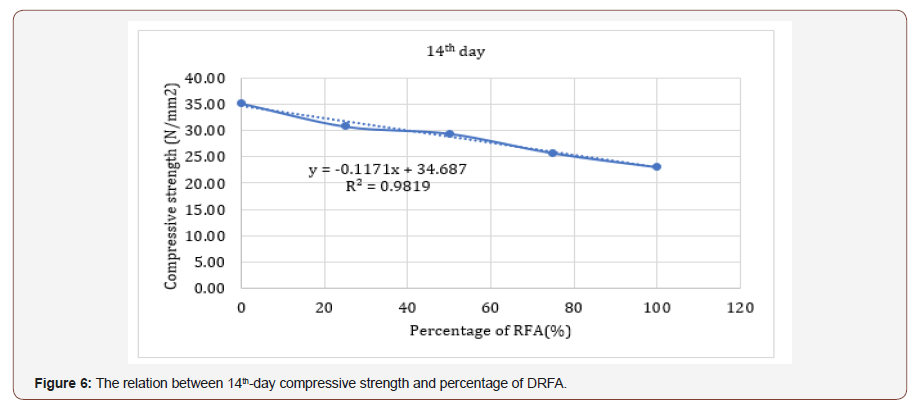
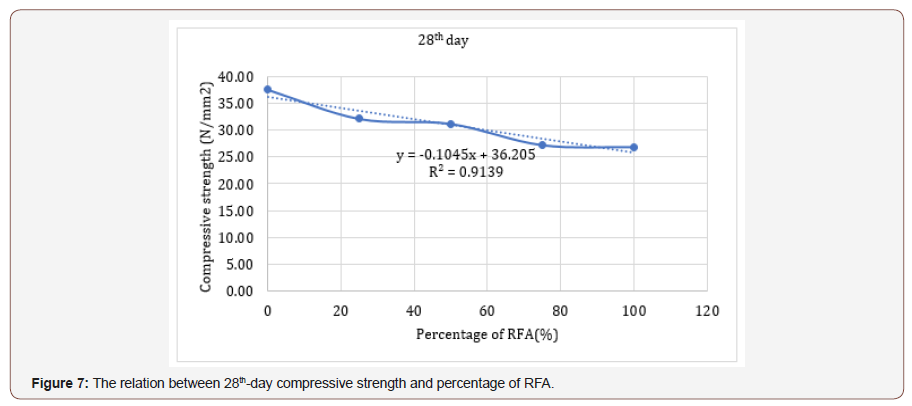
The error bar for the compressive strength of 7th day, 14th day and 28th day are shown below in Figures 8,9&10. This show how much the measurement of the samples are spread out from the average result. If the value of the standard deviation is less than 1, that is low variance, and if the standard deviation is greater than 1, the samples were spread out. From the figures, the values of the three samples were closer to each other.
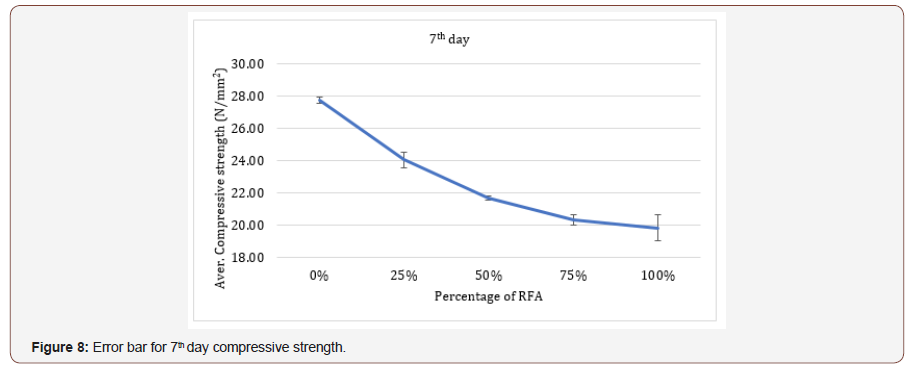

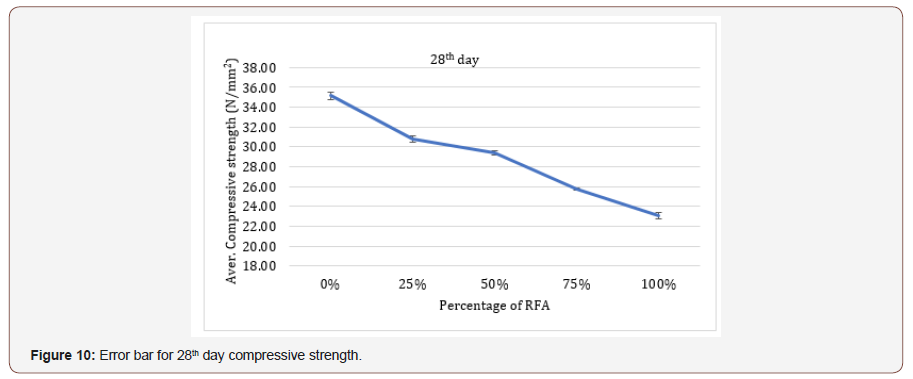
Conclusion
In this research, the suitability of using RFA from demolished HCB in new concrete production and the properties of RFA as compared to natural river sand was examined. The effect of RFA on workability, density, and compressive strength of C-25 MPa was also checked. Generally, the RFA has low physical properties than river sand but within required limits of ASTM standards.
• The recycled fine aggregate has high silt content (14.2%), which is higher than desired by ES standard (6%). It has to be washed to reduce the silt content to the desired level, which is below 6%.
• The recycled fine aggregate has high water absorption capacity due to old mortar attached on the surface as well as the fine particles from cement.
• Using RFA as Natural River sand replacement has decreased the unit weight of the concrete slightly as a percentage of replacement increased.
• The compressive strength decreased as the percentage replacement of RFA increased. The RFA can replace the river sand up to 50 %, which may reduce the utilization of the river sand by 50%.
• Using recycled fine aggregate from demolished HCB in Ethiopia can also help in the reduction of demolished waste disposal to the environment as landfill.
• Using recycled fine aggregate in C- 25 concrete up to 50% will reduce the river sand mining since C- 25 concrete is commonly used concrete in Ethiopia.
• This research has advantages in initiating the local construction sectors and material manufacturers to use demolished wastes in new concrete production since the experiment was performed in Ethiopia in local technology.
Therefore, form this research work, it can be concluded that the demolished HCB can be used as RFA to replace river sand in C-25 concrete production in Ethiopia and can be used up to 50% replacement percentage [21]. And this research can benefit in conserving the non-recyclable natural resources and environmental protection from demolition waste disposal.
Recommendation
• Further investigation on the cost of recycling C&D wastes as compared to the cost of natural river sand have to be investigated.
• The RFA can be used up to 50% by replacing natural river sand, but the specific application area has to be further investigated.
• Investigation on C&D waste generation rate in Ethiopia.
To read more about this article...Open access Journal of of Engineering Sciences
Please follow the URL to access more information about this article
To know more about our Journals...Iris Publishers
No comments:
Post a Comment