Authored by Seongwoo Woo*,
Abstract
To improve the life of mechanical product, parametric Accelerated Life Testing (ALT) as reliability methodology proposes to assess the design of mechanical products subjected to repeated loads, based on (generalized) life-stress formulation and sample size equation. It will help an engineer to reveal the design defects of the mechanical product which making a critical influence on product reliability for the design procedure. Eventually, companies can circumvent product recalls due to the design flaws from the marketplace. As an experiment example, the redesign of compressor in a domestic refrigerator was studied.
Keywords: Parametric ALT; Mechanical system; Compressor; Fatigue; Design defects
Introduction
The mechanical systems such as automobile, airplane, and refrigerator run power to fulfill a task which necessitates forces and movement and yield mechanical advantages by properly adapting system mechanisms. For instance, utilizing the vaporcompression refrigeration system, a refrigerator dispenses chilled air from the evaporator to the refrigerator and freezer department. As consumers want a refrigerator which have good performance and reliability, compressor in a vapor-compression refrigerating cycle was designed to increase pressure from evaporator (low) to condenser (high). If there is a design defect in the system where the (random) loads are subjected, compressor will suddenly stop in its predicted life. After recognizing the design flaws by reliability testing, an engineer could optimally design. This investigation suggests a parametric ALT as systematic reliability method which could be applied to mechanical products. It covers: (1) a parametric ALT strategy, (2) a load examination, (3) a tailored ALTs with the design alternations, and (4) an evaluation of whether the product design(s) fulfil the objective BX lifetime. As a case study, we will examine as following: the redesign of refrigerator compressor.
Parametric ALT in Mechanical System
Linear transport processes are stated as follows:

Solid-state diffusion of impurities in silicon, J, could be formulated as

If Equation (2) puts a reverse function, the life-stress (LS) prototype could be restated as:

The sine hyperbolic form [sinh(aS)]-1 in Equation (3) has characteristics as follows: 1) (S)-1 at the beginning has some linear effect, 2) (S)-n has what is formed as a middle effect, and 3) (eas-1) in the end is high. Because an ALT in the medium range is normally carried out, Equation (4) could be expressed as:

To achieve the acceleration factor (AF), which could be expressed as the proportion between the elevated stress quantities and normal operation conditions, it could be modified to combine with the effort idea:

To attain the mission cycle of an ALT, sample size formulation with Equation (5) might be stated as [1]:

System Subjected to Repeated Pressure Loads
As consumer utilizes the refrigerator, one would store food fresh for a long time. For this purpose, the vapor-compression refrigerator cycle is designed. Compressor is a key component to increase pressure from low to high (Figure 1).
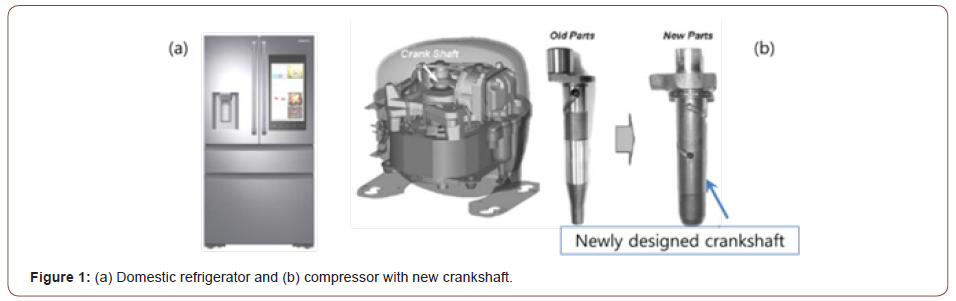
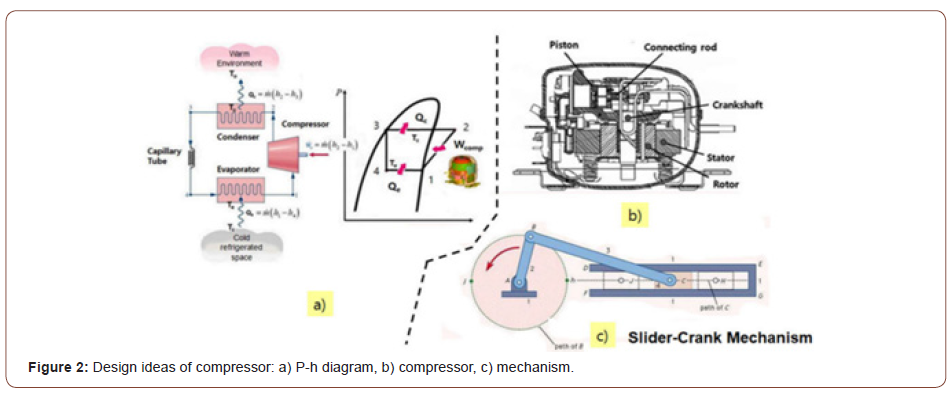
From the marketplace, compressor in a domestic refrigerator were stopping due to design defects. Formed on the consumer working states, compressor was subjected to different pressure loading in vapor-compression refrigeration cycle (Figure 2). The conservation of mass in capillary might be define

The conservation of energy in condenser and evaporator might be defined as


We can determine the mass flow rate m , the condenser temperature Tc , and the condenser temperature Te , from Equations (7) ~ (9). Under the same working conditions, the lifestress formulation might be expressed as:

We recognized that system lifetime relies on exerted impact load. Consequently, the acceleration factor (AF) in Equation (5) could be defined as

For the worst case, the dome temp. in the compressor was 90 ℃ and the pressure range in a refrigeration cycle was 1.07 MPa. For the ALTs the dome temperature was 120 ℃ and pressure range was 1.96 MPa. Using a cumulative damage exponent, λ, of 2.0, the acceleration factor (AF) was calculated to be approximately 4.58 from Equation (11).
For B1 life of 10 years, the mission cycles for one hundred samples computed from Equation (6) were about 19,000 cycles if the shape parameter was presumed to have 2.0. We thus can modify the problematic designs of compressor after identifying them.
Results and Conclusion
In the first ALT, compressor locked due to lubrication at 7,500 cycles and 10,000 cycles. As comparing the problematic product from the marketplace and that from 1st ALT, we recognized that the failure pattern in the first ALT were alike to those attained from the marketplace (Figure 3).
The compressor in both the market products and 1st ALT test samples locked on the surface of crankshaft. We recognized that the design defects of the compressor originated from a) no lubrication areas b) low starting RPM c) material. To obtain adequate mechanical fatigue strength against repetitive pressure loading, the problematic compressor was altered as follows (Figure 4).
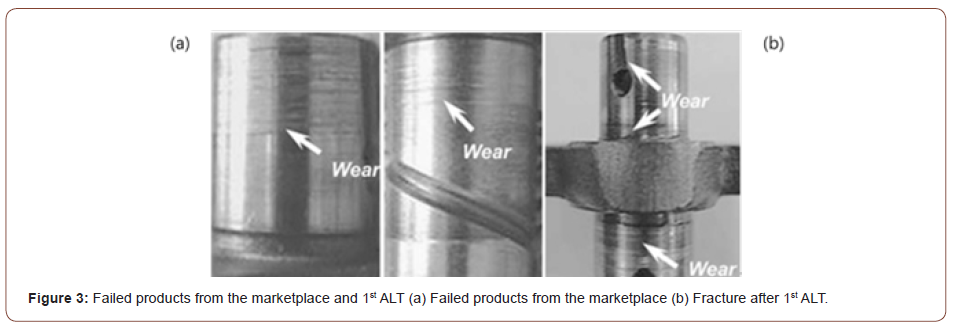
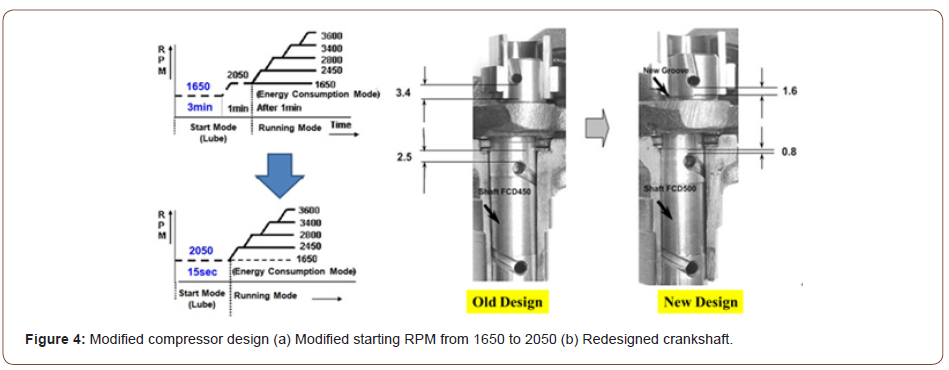
In the second ALT, the crankshaft wear was found at 19,000 cycles. We recognized that the root cause of this failure originated from interference between the thrust washer and crankshaft due to narrow clearance. As an action plans, the clearance between the crankshaft and thrust washer increased from 0.141 to 0.480 (Figure 5).
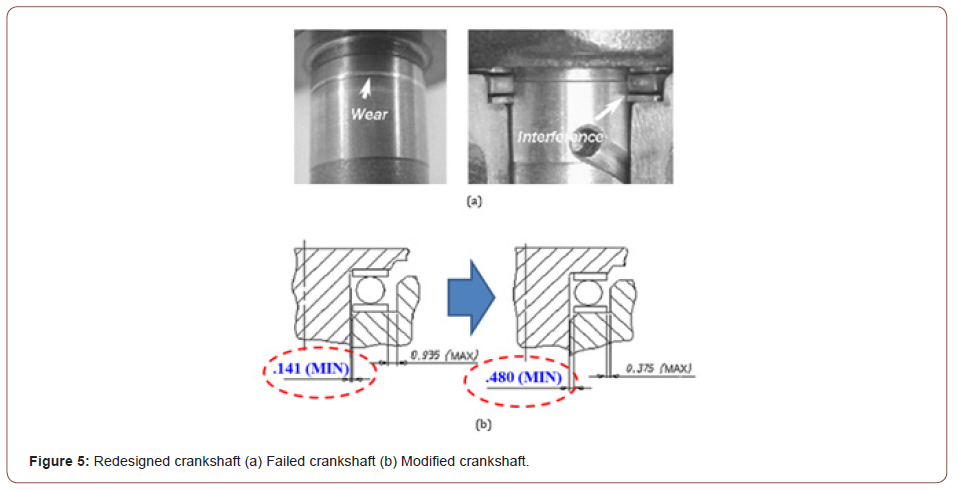
With the design modifications, the compressor in domestic refrigerator could correctly work to fulfil the reliability requirement during its life because there were no issues until 19,000 mission cycles. After three parametric ALTs with design modifications, the life of compressor was ensured to be B1 life 10.0 years.
To read more about this article...Open access Journal of Modern Concepts in Material Science
Please follow the URL to access more information about this article
To know more about our Journals...Iris Publishers
To know about Open Access Publishers
No comments:
Post a Comment