Authored by Renxiang Lu*,
Abstract
The application of Fiber Bragg Grating (FBG) technology for purposes of diagnostic field testing on steel girder bridges is discussed in this paper based on the authors experience in field tests of highway bridges. The primary benefit of the FBG technology is the ability to have many sensors (strain gages) multiplexed in a single fiber optic line. In practice, the FBG system is problematic for field conditions of a typical highway bridge. In field tests, measured FBG data showed that the strain histories obtained for a load immediately above the girder of interest were accurate, but the accuracy of the strain histories decreases for adjacent girders as the transverse distance from the load increased. Moreover, protective measures are necessary for FBG systems to be utilized in highway bridge field testing.
Keywords: Diagnostic bridge field testing; Fiber optics technology; Strain gages
Introduction
In conventional practice, highway bridge design includes conservatism in terms of life-safety. Additional stiffness due to curbs and railings [1], differences in lateral and longitudinal load distribution [2], and unintended composite action between girders and slab [3], can lead to an overly conservative design. As a result, the actual load capacity may be underestimated in routine design. To address this matter, diagnostic field tests can be used to determine the actual capacity of highway bridges and to avoid premature actions, such as posting load limits, enacting repairs, or rerouting traffic [4]. Diagnostic field tests can employ either conventional foil gages or fiber optic sensors. Fiber Bragg Grating (FBG) technology is a sub-category of the discrete fiber optics technology in which readings are only collected at discrete locations [5]. An FBG sensor is a periodic structure that consists of gratings made of silica and acts as a mirror for incoming light [6]. Figure 1 illustrates how FBG technology works. When it interacts with light, a narrow spectral band (wavelength) is reflected to the source while the remaining bands are transmitted through the grating [7]. When the structure is subjected to strain (mechanical or temperature), the spacing of the grating is modified which induces changes on the reflected and transmitted spectral bands. Based on the difference between the wavelengths and properties of the FBG sensor and host material, the induced strain can be back calculated [6]. Since this technology relies on interferometric principles, many sensors (strain gages) can be attached in the same fiber optic line (“multiplexed”) and the respective readings decoded, provided the reflected light spectrum from each sensor is different (Figure 1).
The objective of this paper is to discuss the applicability of FBG technology as a diagnostic field test system for highway bridges. The discussion is based on the authors experience in conducting diagnostic field tests on steel girder highway bridges. Although the discussion focuses on steel girder bridges, it is likely that many of the aspects discussed would also be applicable to other types of bridge superstructures.

Components
For a diagnostic field test, the following components are required: FBG strain and temperature gages, bare fibers and fiber optic connectors, and a data acquisition system. The FBG strain and temperature gages are covered by a steel casing that provides protection to the gratings. Due to the sensitivity of the fiber optics to strain induced by temperature, temperature gages are also multiplexed and placed adjacent to the strain gages. Besides the multiplexing of strain and temperature gages, additional fiber optic lines are also needed: bare fibers are needed to extend the strain gages to the locations of interest for the field testing, and fibers ended with a connector are needed to connect the strain gages to the data acquisition system. These fiber optic lines are composed of three parts: core, cladding and coating. The core is the central layer made of silica in which light travels through with constant reflection. The cladding is the middle layer that envelopes the core and has a lower refractive index in order to make refraction happen according to the Snell’s Law [8]. The coating is the outer layer and protects the core and cladding from physical damages and microbendings. Kevlar is also found between the cladding and coating to provide additional resistance against bending and crushing. The data acquisition system is responsible for acting as the light source and able to store data and transmit to a computer for analysis.
To assemble the different fiber optic lines (known as “splicing”), an arc fusion core alignment splicer is used. For the assembly, the coating and cladding of the fiber optic lines are first manually removed, and the core is cleaved and fused in the splicer. A plastic sleeve inserted before the fusion is slid to the fusing point to provide reinforcement to the singularity. A detailed description of this procedure is provided elsewhere [9]. Strain gages can be installed using adhesives or they can be welded to the host material. In the authors experience, welding is not preferred for steel girder highway bridges because of the potential damage welding may cause to the girder. When installing the gages using adhesives, a two-part glue (resin and curing agent) is applied. Before the application, the paint on the bridge girder needs to be removed, and oxides on the steel surface need to be removed by applying a solution of conditioner and neutralizer.
Installation
Installation of the FBG system in the field is challenging. For example, in the tests conducted by the authors, even though the length of each splice between fiber optic lines was estimated in advance in the laboratory, the actual required length in the field differs. Shorter lines are a problem because they required splices, and a good splice is much more difficult to achieve in the field compared to a lab environment. Furthermore, although the fiber optic lines are protected with coating and Kevlar, they are easily damaged during installation. In practice, damage usually occurs near the transition between one girder to another through the bridge cross-frames, where the bending radius is relatively tight (the fiber optic lines needed to be extended to all girders of the bridge). Singularities of the arc splices are fragile points of the system. Despite having the sleeves covering the fusion points, these singularities are not as flexible and cannot be bent as the remaining portions of the fiber optic lines. This problem can be exacerbated when transporting the FBG system to the bridge site. These problems have a negative impact on the system as the data after the damaged fiber optic line is no longer able to be detected by the data acquisition system. As a consequence, this aspect of installation is a critical downside of the multiplexing property of the FBG technology. A possible remedy for this problem is to conduct splicing of the fiber optic lines in-situ. However, conducting this task may be difficult and time consuming because the fusion of two lines needs to be precise and free of debris (the splicer will automatically reject non-conforming fibers). Adhesives are problematic for bridges. Although the glue applied on the strain gages works well under controlled environmental conditions, it loses its effectiveness in-situ after a couple of hours. Aggravated by the temperature changes, poor adhesion is compounded by steel surfaces that are uneven due to initial imperfections. Improper adhesion can cause the gage to incorrectly measure strain. In situations where only part of the strain gage was attached to the bridge, the gage needs to be removed and discarded, potentially causing the entire fiber optic line to be repaired or also discarded. As an alternative to adhesives, the FBG gages can be fastened mechanically to the girder, using a C-clamp for example. However, C-clamps require a free edge. Thus, the outer portion of the bottom flange can be instrumented, but not locations, such as the girder web. In addition, gages with C-clamps are more noticeable and less discrete compared adhered gages and are susceptible to vandalism. Similarly, the entire FBG system is prone to interference from wildlife.
Accuracy
The accuracy of FBG data can be determined by comparing strain histories obtained by the FBG system with a redundant sensor system. The authors used conventional (Wheatstone Bridge) strain gages that are hardened to protect it against adverse environment. Figure 2 shows a comparison of the FBG and conventional strain histories. The FBG measured response is accurate for a girder near the load (Figure 2a), but often inaccurate for a girder away from the load (Figure 2b). Moreover, since the magnitude of the strain is smaller for girders farther away from the load, the measured strain is sensitive to the inherent noise in the FBG signal. The noise in the FBG system can be caused by the glue used to bond the strain gages to the girders. The variation of temperature or inaccurate mix of the resin and curing agent are probable sources for this issue. Nevertheless, it should be pointed out that despite the inconsistencies found in the FBG system for when the girder is away from the load, the measurement in the distant girders has negligible influence on the estimation of the actual bridge load rating because the strains obtained are much smaller than the strains obtained in the girders immediate to the load (Figure 2).
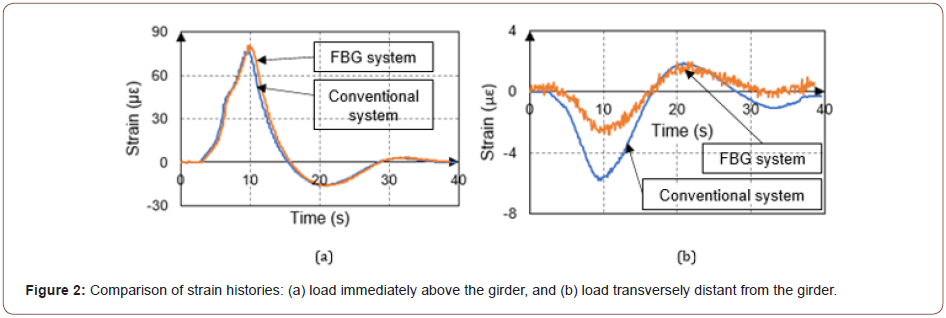
Conclusion
FBG technology is appealing for diagnostic field testing of highway bridges for three reasons: first, the fiber optic lines can be multiplexed, second, the fiber optic lines can be custom fit using arc fusion splicing, and third the FBG sensors have been shown to be accurate for large-magnitude strains. However, based the authors experience, these advantages are outweighed by other aspects. Fiber optic lines lack robustness (they are easily damaged and sensitive to installation, in particular the curvature of the line). FBG gages are also difficult to install in the field properly using adhesives. Singularities of the splicing and the bare fiber optic lines are also an issue. Even though the bare lines are protected with sleeves, coating, and Kevlar, actual performance under field conditions tends to be poor. Since FBG strain gages are attached in a multiplexed series, the breakage of one fiber optic line in a particular point renders a loss of data from all strain gages beyond the breakage point. This problem may not always be observed visually and may not be detected until data collection. Although adhesives can be replaced by C-clamps in some situations, C-clamps are vulnerable to vandalism and do not work for girder webs. In summary, in the authors, opinion, FBG technology is a promising but underdeveloped solution for diagnostic field tests of bridges. Unless protective measures for the fiber optic lines and enhanced bonding agents under field conditions are devised, the disadvantages of FBG systems will outweigh the benefits. Further research to improve the robustness of FBG technology is needed to make FBG systems a viable way to measure strain under in-situ conditions for steel girder highway bridges.
To read more about this article...Open access Journal of Civil & Structural Engineering
Please follow the URL to access more information about this article
https://irispublishers.com/ctcse/fulltext/discussion-of-fiber-bragg-grating-technology-applicability-on-diagnostic-field-testing-of-steel-girder-bridges.ID.000681.php
To know more about our Journals...Iris Publishers
To know about Open Access Publishers
No comments:
Post a Comment